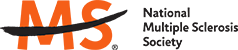
Job Information
Newmont data-careersite-propertyid="title" class="rtltextaligneligible">Underground Maintenance Dewatering Supervisor in United States
data-careersite-propertyid="title" class="rtltextaligneligible">Underground Maintenance Dewatering Supervisor
Date: Apr 23, 2024
Location:
Ahafo, GH
Workplace Type: Onsite
Additional Responsibilities:
About This Role:
- To coordinate, direct and lend technical support to all on-site water management operations and maintenance activities, in a safe manner, and coordinate resource allocations to effectively attain goals and realize production plans.
In This Role You Will:
Dewatering Operations and Maintenance Execution
Receive guidance from the General Foreman – Projects for optimal approaches to water treatment and dewatering.
Oversee the construction and laying of pipelines into the pit.
Install physical critical controls (i.e. demarcations), prior to dewatering activities.
Coordinate and pair the operators and pump men with the relevant equipment required to execute tasks.
Schedule and supervise all dewatering and water treatment activities, by overseeing and evaluating works-in-progress
and assure that all activities meet specifications, codes and regulations.
Identify opportunities for both short and long-term interval controls, based on the mine dewatering plan, and make any necessary adjustments and changes to the shift, to meet daily target projections.
Oversee all water treatment activities such as:
areas to be dewatered.
rate of pumping required.
distribution of labour, supplies and equipment.
Oversee all contractors assigned to designated mine dewatering work areas within the department.
Provide technical guidance and transfer of knowledge to the operators and pump men through active coaching and mentoring.
Examine the extent to which issued instructions are being followed and escalate any non-adherences to the General Foreman.
Hold operators and maintainers accountable for the work completed by:
administering discipline and facilitating corrective actions.
monitoring dewatering equipment performance, in line with agreed KPI’s.
conducting QA/QC’s on installed piping.
explaining the mine dewatering plan to the crew and providing clear instructions.
implementing continuous improvement initiatives.
managing shift changeovers between crews.
Analyse daily dewatering production and cost data to confirm that the department is operating within overall costing projections and budget; report any variances from costs and budgets.
Make provision for capital budgeting for maintenance tools such as welders, trucks, air compressors, generators, and other associated tools.
Oversee and coordinate the implementation of pipe fusion activities.
Establish pump installations to pump water from the pit floor, ahead of mining operations activities.
Oversee the coordination of water supply to Newmont water trucks and initiate the pump system to avail water supply to the mine operation.
Oversee the steady supply of clean water to process
Coordinate the maintenance of dewatering and water with the Maintenance Department.
Monitor stock levels of consumables, identify critical items, place orders and manage relevant contractors in the provision of such items.
Provide feedback reports regarding mine dewatering activities to the General Foreman – Projects for review.
Maintain accurate records and archives of all mine dewatering activities
Maintain a high housekeeping standard in the areas of underground mine infrastructure.
Additional Responsibilities:
Dewatering Operations and Maintenance Planning
Execute short, medium and long-term underground mine dewatering and water treatment plans.
Implement goals, objectives, policies, procedures and work standards for the area.
Oversee and coordinate the weekly plan for the initiating of dewatering schedules and activities.
Lead and supervise shift mine dewatering teams to achieve production targets.
Coordinate, prioritise and assign tasks for dewatering activities to meet shift target goals.
Provide technical expertise and input into the dewatering plan.
Conduct pre-water treatment assessments within the pit to determine water quality and ground stability.
Send all dewatering requisition requests to the General Foreman for review and obtain sign-off from both the General Foreman and Mine Maintenance Superintendent.
Provide input into daily operational issues regarding areas affected to the General Foreman / Management.
Provide input into daily operational and make changes as directed by the General Foreman / P Operations Management.
Manage and control costs within own area, where possible (i.e. reduce waste, improve operational control).
Request services from other departments as required.
Participate in continuous improvement programs which will assist in enhancing the performance of the process plant operation.
Coordinate and execute smaller projects in the undergroundarea by following the change management procedure.
Complete all tasks identified in the Processing Operations MOS Elements to the specified quality and timeliness as assigned to this role.
Provide input into the development and review of the underground maintenance STPs, management plans and operating procedures, guidelines.
Stakeholder Management and Engagement
Coordinate with the Load and Haul team for the establishment and placement of dewatering infrastructure.
Collaborate with Mine Maintenance to confirm pump availability and undertake necessary troubleshooting activities, when required.
Liaise with various Ghanaian government authorities to assure that all national codes and standards are met and complied with in assigned blasting activities.
Coordinate activities with all departments to ensure continuity of the total mine operation.
Obtain suggestions from other Newmont departments, in identifying opportunities for improving dewatering and water treatment efficiency and productivity.
Liaise with the Training Department to arrange the receipt of training schedules and times for the national workforce.
Oversee that dewatering and water treatment shift work meets established statutory standards.
Additional Responsibilities:
Dewatering Optimisation and Continuous Improvement
Advise on best practices relating to dewatering and water management to improve productivity.
Investigate, report and escalate all accidents and incidents occurring in the shift to the General Foreman – Projects for immediate review.
Participate in the weekly shutdown and commitment meetings to be informed on the maintenance scheduled activities and execution plans.
Health and Safety Management
Assist with the adherence of fixed plant maintenance and operation to all HSLP, Environment and Social Responsibility requirements under Newmont’s Integrated Management System, Newmont vision and values.
Oversee and manage compliance with all statutory requirements for the underground mine and associated mechanical infrastructure through the delivery of inspections, audits and reports.
Assist with the implementation of applicable health and safety regulations and compliance programs.
Accept responsibility for the health and safety of every employee under or assigned to his / her supervision.
Conduct and attend periodic safety meetings, inspections and audits.
Support and conduct risk assessments for tasks and provide expert advice on the safe operation and maintenance of fixed plant underground infrastructure.
Actively promote safety in the workplace both within and external to the fixed plant maintenance team.
Revert to the Engineering team to potentially change shift plans for a particular area, arising out of work hazard detection.
Conduct periodic safety meetings and safety inspections.
Lead daily pre-shift staff debriefings.
Attend monthly safety inspection and meetings
Staff Supervision
Create a suitable shift work environment to motivate Operators to achieve optimum effectiveness and productivity.
Supervise all direct reports by:
participating in the recruitment and selection of staff.
recommending the selection of new staff.
conducting crew assessments.
developing the team to perform at their best capabilities.
contributing to performance appraisals.
participating in team performance management calibrations.
managing available skill sets.
recommending further / relevant training courses and development actions in accordance with Newmont’s people development program(s).
implementing training for staff.
coaching and mentoring staff.
disciplining poor performance or actions.
enhancing communication with staff through regular feedback, contact, meetings and briefings.
Your Training, Skills & Experience Checklist:
Formal Qualification (including Professional Registrations):
Bachelor’s degree or Diploma in Mechanical Engineering or related field.
Mine Foreman Certificate.
Sectional Engineering Certification.
Additional Knowledge:
Advanced knowledge of industrial work management processes.
Advanced knowledge of defect elimination methodologies and their interpretation.
Knowledge of and experience with Reliability Centered Maintenance programs.
Strong working knowledge in the operation and maintenance of pumps and dewatering systems is highly desirable.
Advanced knowledge of the statutory regulations relevant to safety and the environment for the mining industry.
Proven working knowledge of CMMS programs.
Strong knowledge of planning and scheduling maintenance activities.
Fair knowledge in process water management and water balance.
Experience:
Minimum of 4 – 5 years’ mine dewatering/civil works experience in large open pit mining environments, of which at least 2 – 3 years’ experience should be in a shift supervisory capacity.
Proven experience with the installation, commissioning, maintenance, servicing, inspection and repair of mechanical apparatus and installations in a large scale mining or heavy industry operation
Underground mining experience is highly desirable.
Technical Skills:
Advanced analytical and problem-solving skills.
Advanced communication (written and verbal) and interpersonal skills.
Advanced computer literacy skills - MS Office (Word, Excel, PowerPoint and Outlook), and SAP.
Advanced information monitoring and management skills.
Advanced planning, organizing and prioritizing skills.
Strong business continuity management skills.
Strong capacity planning skills.
Strong decision-making skills.
Strong time management skills.
Strong conflict management and influencing skills.
Strong project management skills.
Strong personnel administration skills.
Sound needs analysis.
Sound change management skills
Behavioural Attributes:
Accuracy.
Customer focused.
Deadline driven.
Detail oriented.
Goal Oriented.
Initiating.
Leadership.
Proactive.
Reliable and independent.
Safety conscious.
Team player.
Technically Inclined.
Working Conditions:
The Position is located in the Ahafo South mine site.
We understand no candidate will meet every single desired qualification. If your experience looks a little different from what we’ve identified and you think you can bring value to the role, we’d love to learn more about you!