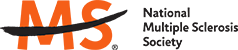
Job Information
Edgewell Personal Care Brands, LLC Senior Manufacturing Engineer in Sidney, Ohio
We are a company of people—a global team of 6,800 visionaries, doers, and makers. With more than 25 brands in our portfolio, we bring joy to more than 50 countries, keeping a keen eye on efficiency and sustainability. We’re also passionate about maintaining a diverse, inclusive, and respectful environment where our teammates can thrive.
Position Summary
Edgewell is seeking to hire an Senior Manufacturing Engineer at our manufacturing facility located in Sidney, Oh. In this position, you will manage and coordinate the implementation of batching and converting process improvements. This results in daily operation efficiency improvements within the plant environment. The Senior Manufacturing Engineer provides technical knowledge in the trouble shooting of operational problems within the facility. Work with the operational team to improve plant-manufacturing efficiencies and provide support in the continuous improvement process of finished goods produced within the business. Provide support for smooth and timely introductions of new and modified packages.
Essential Functions
The essential accountability of this position is to design and execute projects in support of business needs and objectives.
Provide daily technical support to operations staff in the trouble shooting of equipment and processes in an FDA regulated environment.
Develops, evaluates, and improves manufacturing methods.
Analyzes and plans work force utilization, space requirements, and workflow, and designs layout of equipment and workspace for maximum efficiency.
Estimates production times, staffing requirements, and related costs to provide information for management decisions.
Resolve deviation reports concerning product or material with plant personnel including maintenance personnel to direct equipment adjustments.
Distributes product/part drawings to appropriate plant personnel.
Manage the delivery process of equipment modifications within the manufacturing environment.
Work with project team to investigate and implement equipment and process changes to expand and develop the business.
Initiate and implement improvements to current equipment to increase efficiency and optimize manufacturing costs.
Provide technical assistance to plant maintenance in the modification of plant equipment.
Maintain current knowledge of Lean Manufacturing methodologies, prepare capital request, cost justifications to support recommendations.
Prioritize and implement schedules for assigned projects using appropriate planning methods and facilitate project implementation.
Serve as a facilitator coach for teams during Kaizen events and follow up to assist supervisors to sustain work improvement.
Prepare final equipment specification package and equipment shakedown, qualification and verification test procedures for new and modified packaging equipment.
Create Capital Asset Request (CAR) for the purchase of new equipment and facility improvements. The CAR process includes calculating the cost of new equipment and justifying the purchase by calculating savings and efficiency in a formal written document.
Implement cost benefits through equipment improvements resulting in more efficient packaging operation. Active participation in competitive product and value analysis programs to suggest and follow through on new opportunities.
Work across departmental lines to establish and develop equipment suppliers, which will continually contribute new and improved packaging converting ideas.
Ensures that new and existing equipment is compliant with all applicable government regulations (e.g. DOT, EPA, FDA, OSHA, etc.)
Assist in the development of long range and short-range capital expenditure program and prepare the necessary capital project analyses to support site capital plans.
Lead the development of packaging process improvements, which improve plant efficiencies.
Actively participate in plant cost savings, safety and quality activities.
Maintain current technical knowledge in the engineering field.
Project Management Skills.
Provide Accounting with NPD support.
Travel to support suppliers as required.
Perform other similar duties as assigned.
Required Skills and Experience
Bachelor’s degree in manufacturing / Industrial Engineering or related field from a four-year college or university. Five+ years related experience and/or equivalent combination of education and experience.
Prefer knowledge of Lean Manufacturing methodologies and a proven track record with application.
Experience:
Minimum of 5 years manufacturing experience, preferably in a high speed, cGMP environment.
Other Required Knowledge, Skills & Abilities:
Prior experience with major equipment relocations including start up, debug and validation execution.
Good communications skills – must be able to develop specifications, proposals, RFP’s and presentations and communicate effectively within the organization, both laterally and vertically.
Working knowledge of “AutoCAD” or equivalent CAD system, MS Project, and MS Office.
Results oriented, hands-on individual, with the ability to lead sub-groups, task forces or teams to effectively solve machinery problems ranging from simple (slight modification/addition of single component) to complex (total re-design) on high-speed, high-volume machinery.
Ability to analyze, design, plan and manage equipment installations.
Preferred Skills
Inquisitive personality and willingness to work outside of their comfort zone.
Proven ability to manage a project from start to finish.
Experience with Root Cause Analysis techniques and Problem-Solving techniques.
Experience with mentoring less experienced employees or students in a technical area
Lean manufacturing / Six Sigma background
Working Relationships
Reports to Plant Manager
Key relationships internally will include:
Manufacturing and Quality Assurance.
Product Development and Innovation Teams.
Program Management, Tech Transfer
Professional and technical staff in the Department
Work Environment
Some travel may be required.
Work on night shifts and weekends may be required to support business needs.
Exposure to health risks or conditions that may require the use of Personal Protective Equipment.
The salary range for this position is $84,000 - $126,000. Actual base salary offered to a candidate may vary based upon factors including, but not limited to, relevant experience, time in role, base salary of internal peers, prior performance, business sector, and geographic location. In addition to base salary, the competitive compensation package may include, depending on the role, participation in an incentive program linked to performance.
#LI-DR1
Edgewell is an equal opportunity employer. We do all we can to create a collaborative and diverse global team, where good ideas can thrive, and our colleagues can learn and lead. We prohibit discrimination based on age, color, disability, marital or parental status, national origin, race, religion, sex, sexual orientation, gender identity, veteran status or any legally protected status in accordance with applicable federal, state and local laws. We listen deeply and speak directly to create an environment that’s open to difference. We aim to bring joy to not only the products we create and the people we serve, but our colleagues across the globe too.
Edgewell Personal Care Brands, LLC
-
- Edgewell Personal Care Brands, LLC Jobs