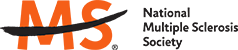
Job Information
Winland Foods Maintenance Mechanic II (3rd Shift) in San Antonio, Texas
Advanced and in-depth knowledge of most food production equipment and infrastructure. Conducts machine set-up, troubleshooting, repairs and preventative maintenance services to all plant equipment.
Employee Type:
Full time
Location:
TX San Antonio
Job Type:
Production Maintenance
Job Posting Title:
Maintenance Mechanic II (3rd Shift)
Job Description:
Performs highly diversified and complex duties to install and maintain production equipment and the plant facility’s equipment including, but not limited to, mechanical, electrical, pneumatic and hydraulic troubleshooting, repair of packaging and production machines, etc.
Diagnoses and troubleshoots basic and complex problems to component level, replaces and repairs parts, tests and makes adjustments as needed
Provides emergency/unscheduled repairs of assigned production equipment during production and performs PM’s according to schedule and during gaps or downtime
Assist with production startups and change-overs, as needed
Performs a full range of basic and complex machinist duties and responsibilities
Reads and interprets equipment manuals and work orders to perform required maintenance and service
Reads and interprets electrical schematics, blueprints, drawings and wiring diagrams
Works as a team and independently on basic and complex maintenance projects including new equipment installs and rebuilds
Participates in Process Improvement Teams (PITs) as assigned
Strong working knowledge with cutting torch, grinder, drill press, a variety of hand and power tools, electric meters and material handling equipment
Complies with Company and OSHA Safety and Health rules and maintain a clean and orderly work area
Completes required paperwork accurately and thoroughly
Accesses computer to look up part numbers and parts; also completed administrative duties through CMMS system
Assist contractors as needed
Assist with mentoring and training new hires and less experienced Mechanics/Technicians, and helps others including but not limited to Plant Leads, Supervisors, Machine Operators, etc.
Performs other duties as assigned
SAFETY AND QUALITY:
Understands equipment hazards to prevent injury to self and others – understands company policies on safety and follow procedures – GMP’s, (Good Manufacturing Practices), HACCP (Hazard Analysis Critical Control Point), PPE (Personal Protective Equipment) Lock-out Tag-out
Reports any food safety problems or potentially unsafe practices/conditions to the Supervisor
Is able to safely lift items up to 50lbs – motors, parts - asks for help when lifting heavier items
Recommends changes to improve safety standards
Is certified to use the motorized Pallet Jack, Fork Lift, Scissor Lift, Lock-out Tag-out – ensures safe operation of all machinery, tools and equipment
Maintains proper housekeeping and safety standards
WORK ENVIRONMENT:
May be assigned to work in extremely cold or hot conditions
Works in various environments including, but not limited to, production, buildings, and grounds.
Most positions are located in areas with loud noise and will require the employee to wear protective ear plugs
Other conditions include dust, wet floors, occasional smoke and fumes from cleaning chemicals
Main activities will be walking, lifting, standing, sitting, bending, pulling, pushing, reaching and climbing. Some crawling, kneeling and reaching overhead work will also be required
May occasionally be required to work in cramped or confined spaces
May occasionally be required to work in high places – where fall protection is required.
SCOPE:
These positions have no supervisory responsibilities
Works closely with Plant Leads and Supervisors, Machine Operators, Fabricators and less experienced Mechanics
COMPETENCIES:
Mechanical – strong understanding of equipment operations – troubleshoots and modifies as needed, pneumatic, hydraulic and mechanical power transfers, including but not limited to, gearboxes, brakes, clutches, bearings, sprockets, gears, pulleys, pumps, chains, and shafts, etc. – identifies parts for repair or replacement or modification – performs thorough PM’s on all equipment – performs daily operational checks of equipment, and constantly monitors efficiency and downtime – helps production with the setup of the equipment. This includes, but
Electrical – understands basic and complex electrical theory (24 volt DC up to 480 AC) and is able to troubleshoot motors, drives, contactors, relays, solenoids, power supplies, valves, photo eyes, sensors, wiring – is able to read electrical schematics and identify components and functions as they apply to specific manufacturing parameters
Rigging – understands weight capacities and lift extensions to be able to lift, move and insert heavy pieces of machinery – able to operate fork lifts, scissor lift, sky lift, etc.
Fabrication – strong working knowledge and ability to fabricate parts from metal and plastic for equipment – welds, cuts with saw, torch or plasma cutter – full working knowledge and experience of welding and fabricating tools and equipment (hand and power)
Oral Communication - Speaks clearly and persuasively in positive or negative situations; listens to other’s ideas/issues; responds well to questions. Effectively presents information in writing, one-on-one and small group situations to customers, clients and other employees
Teamwork - Contributes to building a positive team spirit; puts the success of the team above his/her own interests; supports everyone's efforts to succeed; maintains a positive attitude; generates ideas and suggestions that improve the team’s performance, the efficiency of the process or the quality of the products
Ethics - Treats people from own and other cultures with respect; works with honesty and integrity; upholds organizational values
Dependability - Follows instructions, responds to management direction; commits to long hours of work when necessary to reach goals; is consistently at work and on time
Flexibility and Adaptability – Must be able to deal with sudden changes in scheduling; filling in on other positions to help out when needed
Language skills – Should be able to read and write the necessary documents and procedures in English. In addition, should be able to communicate clearly in English any work direction, instructions or feedback. Ability to speak Spanish is not required but is helpful
Decision-making – Able to handle problems and think through to solutions. Knows when to act independently and when to involve the Supervisor
Mathematical Skills – Able to add, subtract, multiply and divide in all units of measurement, using whole numbers, common fractions and decimals. Ability to compute rate, ratio, and percent
EDUCATION/QUALIFICATIONS:
Advance in-depth knowledge of food production equipment and infrastructure
High school diploma or general education degree (GED); completion of apprenticeship or some college/technical school courses highly desired; AA degree in mechanical, electrical, or industrial maintenance a plus
Prefer three to five years of manufacturing experience with a strong working knowledge in the following areas: hydraulic, pneumatic; mechanical, electrical and industrial skills.
Basic PLC Hardware knowledge and understanding of software and programming
Computer skills, including Microsoft Office, E-mail, and simple database applications
Willingness to work weekends and overtime when required
Able to lift up to 50 lbs
Able to read, write and speak English – bilingual Spanish a plus
It is impossible to list every requirement for, or responsibility of, any position. Similarly, we cannot identify all the skills a position may require since job responsibilities and the Company’s needs may change over time. Therefore, the above job description is not comprehensive or exhaustive. The Company reserves the right to adjust, add to or eliminate any aspect of the above description. The Company also retains the right to require all employees to undertake additional or different job responsibilities when necessary to meet business needs.
EEO Statement:
Winland Foods believes that diversity and inclusion among our teammates is critical to our success as a global company, and we seek to recruit develop, and retain the most talented people from a diverse candidate pool. Winland Foods is committed to providing an environment of mutual respect where equal employment opportunities are available to all applicants and teammates without regard to race, color, religion, sex, pregnancy, national origin, age, physical and mental disability, marital status, sexual orientation, gender identity, gender expression, genetic information, military and veteran status, and any other characteristic protected by applicable law.
Winland Foods is a leading private label food manufacturer of pasta, dry dinners, condiments, syrups, and more with nearly 3,000 employees operating out of 14 production facilities in US, Canada, and Italy.
As a ‘newly’ established company, we are creating the building blocks for an innovative and agile organization that is purpose driven - delivering high quality food to our customers and communities. We foster an environment that encourages all employees to be heard, and values their contributions and ideas.
By joining Winland Foods, you become a part of a new team that values passion, collaboration, and strives to prosper with our customers.
To all recruitment agencies: Winland Foods does not accept unsolicited agency resumes/CVs. Please do not forward resumes/CVs to Winland Foods employees, or any company location(s). Winland Foods is not responsible for any fees related to unsolicited resumes/CVs.
Winland Foods
-
- Winland Foods Jobs