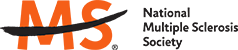
Job Information
TE Connectivity MGR I MFG & PROCESS DVL ENGINEERING in QINGDAO, China
MGR I MFG & PROCESS DVL ENGINEERING
At TE, you will unleash your potential working with people from diverse backgrounds and industries to create a safer, sustainable and more connected world.
Job Overview
TE Connectivity's Manufacturing and Process Development Engineering Teams significantly impact LEANPD driven new product development projects, driving for excellence in existing manufacturing technologies and methods and striving to implement new manufacturing technologies to provide improved process and tolerance control. They act as the binding element between product development and manufacturing engineering, ensuring the effectiveness and efficiency of this critical interface. They support Product Development in the optimization of designs and piece parts for manufacturability by realizing sample tooling/products/prototypes. They also design, develop, and qualify tooling and processes to meet TE quality and production standards, document all processes and tooling in applicable TE systems, support supply chain to verify supplier compliance and capability, initiate and implement programs to continuously improve quality, cost and cycle time and adhere to all appropriate specifications, regulatory requirements and customer requirements.
What your background should look like:
Responsibilities:
Leadership: Provide strategic direction and leadership for the Manufacturing and Process Development Engineering teams.
Operational Strategy and Organizational Development: Contribute to defining operational strategy and develop the organization in support of business strategy, managing complex organizations with multiple sub-functions.
New Product Introduction (NPI): Lead the successful transfer of new products from Engineering to Manufacturing Operations, ensuring seamless integration of processes and systems. Optimize Time to Market for successful new product launches meeting customer targeted timelines.
LEANPD Driven New Product Development: Play a pivotal role in LEANPD driven new product development projects, ensuring strong impact and adherence to Lean principles throughout the process.
Process Leadership and Expertise: Serve as a process leader for stamping, molding, assembly, or other TE manufacturing processes, ensuring optimal performance for quality and output
Cross-functional Collaboration: Collaborate closely with Product Development Engineering, Quality Assurance, Supply Chain, and other departments to ensure alignment and effective communication.
Interface Between Product Development and Manufacturing Engineering: Act as the binding element between product development and manufacturing engineering, ensuring effective communication and collaboration to optimize designs for manufacturability
Process Optimization: Drive continuous improvement initiatives to enhance manufacturing processes, ensuring efficiency, quality, and cost-effectiveness.
Continuous Improvement Initiatives: Initiate and implement programs to continuously improve quality, cost, and cycle time, aligning with TEOA requirements and Best Demonstrated Practices (BDP’s).
Resource Management: Manage resources effectively to meet production schedules and project deadlines, including personnel, equipment, and budget allocation
Performance Monitoring: Establish KPIs and metrics to monitor manufacturing performance and drive continuous improvement efforts.
Talent Development: Mentor and develop engineering talent within the department, fostering a culture of learning and growth.
Knowledge and Expertise in Manufacturing Techniques: Demonstrate expertise in mold tooling, die tooling, machining, and other manufacturing tooling and assembly techniques, optimizing and standardizing processes within the manufacturing environment.
Qualifications:
• Bachelor's degree in a relevant Engineering or Science discipline.
• Management experience within functional/sub-functional areas and knowledge across related functions.
• Proven ability to lead cross-functional teams and drive continuous improvement initiatives.
• Commitment to driving continuous improvement initiatives and implementing best practices to enhance operational efficiency.
• Strong analytical skills with the ability to work on issues of diverse scope and provide input on key issues impacting the function.
• Ability to establish and assure adherence to budgets, schedules, work plans, and performance requirements.
• Ability to thrive in a fast-paced, dynamic environment and effectively manage change.
• Experience with applicable TE systems (SAP, TLM, CAD, etc.) and familiarity with regulatory requirements and industry standards.
• Willingness to travel as needed.
Competencies
Building Effective Teams
Motivating Others
Managing and Measuring Work
Values: Integrity, Accountability, Inclusion, Innovation, Teamwork
SET : Strategy, Execution, Talent (for managers)
Location:
QINGDAO, SD, CN, 266113
City: QINGDAO
State: SD
Country/Region: CN
Travel: Less than 10%
Requisition ID: 123479
Alternative Locations:
Function: Engineering & Technology
TE Connectivity and its subsidiaries, affiliates, and operating units (collectively, the "Company") is committed to providing a work environment that prohibits discrimination on the basis of age, color, disability, ethnicity, marital status, national origin, race, religion, gender, gender identity, sexual orientation, protected veteran status, disability or any other characteristics protected by applicable law or regulation.
TE Connectivity
-
- TE Connectivity Jobs