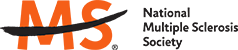
Job Information
Chevron Corporation Mechanical Supervisor in Maracaibo, Venezuela
Total Number of Openings
1
Chevron Venezuela is accepting online applications for the position Mechanical Supervisor through July 17 at 11:59 p.m.
Overview:
Ensures operability, reliability and efficiency of process and pumping units, rotating equipment, production facilities, in conjunction with the timely execution of preventive and diagnose maintenance and corrective maintenance of equipment existing in Boscan Field production facilities. Leads Mechanical groups towards the achievement of safety, operational excellence, costs reduction and high technical competency. Provides mechanical to SCP and MCP's associated to Campo Boscan.
Responsibilities:
Provides supervision and leadership to the JV Maintenance group within area of responsibility, supervising Mechanical Group, Supervisors, and contractors. Ensures that direct reports execute their programmed daily activities (preventive / predictive / diagnostic / failure correction / certification), related to all rotating and mechanical equipment, pumping units in Boscan Field plants and flow stations.
Provides operational excellence leadership and ensures that the activities are executed incident free. Ensures all tasks are performed under work permits with risk analysis and JSA’s. Coordinates with production operations to prioritize maintenance activities. Acquires and allocates resources needed to align maintenance efforts with production goals. Ensures maintenance procedure development, start-up plans, maintenance team readiness, commissioning activities after hand-over, PSSR support, reviews and coordinating multidiscipline teams are coordinated and executed.
Pre-Operations to support design reviews, provide maintenance input into design, maintainability and constructability issues for all equipment and operational processes. Assists with planning and execution of turnaround plans as needed. Support and assist with the preparation of staff training plans. Fosters teamwork and effective communication among peers and cross functional team members. Demonstrates high OE behaviors and upholds all applicable laws and regulations. Extends and fosters safe work practices and procedures to the contractor work groups. Coordinates and supervises mechanical work teams; coordinates planning and development of procedures for startup and continuous operations.
Assists with preparation of the OPEX and CAPEX budgets for Production Operations Maintenance, with clear focus on area of responsibility budget control / management. Assists with preparation of labor forecasts to support near term and projected future organizational capabilities. Drives cost reduction in field mechanical maintenance operations. Monitors mechanical maintenance cost data and provides leadership in such cost optimization efforts. Ensure the development and implementation of a contracting plan (master and individual contracts), to support mechanical maintenance function. Assists with preparation of labor forecasts to support near term and projected future organizational capabilities.
Supports Supply Management / Warehouse on required spare parts/equipment item determination and supports establishment of appropriate inventory to support maintenance programs to be executed. Interface with suppliers to ensure proper quality control of items delivered and in accordance with manufacturer’s specifications.
Manage accomplishment of maintenance program for assigned equipment. Leads the development of updated planned maintenance routines for pumping units and for all installed rotating equipment, such as engines, pumps, compressors, etc. Assists with the implementation of Base Business initiative, FIRM and SAP Maintenance Module to ensure successful implementation of a fully functional CMMS System. Ensures effectiveness of planned maintenance program and coordinates work group’s efforts to drive maximum performance on reliability and operational excellence.
Responsible for drafting the repair, maintenance and overhaul plans for mechanical equipment; organizing and training operators to conduct minor maintenance and periodical minor maintenance for various types of mechanical equipment. Establishes maintenance and repair schemes, sets up PM’s according to time, PdM, etc. and coordinates material plans and daily operating plans.
Actively promotes safety, efficiency, reliability and waste minimization. Accountable for delivering business plan HSE targets.
Fosters an Incident Injury Free Operations (IIF) environment using the Operational Excellence (OE) Management System. Assists with administration of an Operations Health, Environmental & Safety (HES) program that includes, safety training, behavioral based safety observation program, compliance reviews, audits, Root Cause Analysis (RCA’s), emergency preparedness, near-miss/incidents reporting, safety meetings, and process improvement initiatives. Places a strong emphasis on development of the local contractor(s) workforce regarding health, environmental & safety performance. Participates in HAZOP and PSSR. Develops failure analysis of rotating equipment and predictive/diagnostics analysis. Participates in incident investigation committees. Accountable for keeping mechanical maintenance groups technical competency developing, organizing and coordinating appropriate training programs. Actively performs field COEM inspections.
Advises facility engineering group regarding field operations and maintenance needs on new installations / upgrades. Assists Operations and represents Maintenance in multidisciplinary teams for facilities design and capital projects. Interfaces and provides “direct support” for plant operations and Capital Projects. Ensures EM personnel are part of capital projects. Provides input for Peer Reviews, PHAs, FAT, ORR reviews, equipment selection, drawings reviews, equipment preservation, materials / spare parts identification etc. Provides oversight, guidance and supervision as needed to current and future contract companies for successful completion of facilities. Provides feedback – updates to operations supervisory staff for all JV initiated FE projects.
Required Qualifications:
1.- Manage accomplishment of maintenance program for assigned equipment.2.- Leads the development of updated planned maintenance routines for pumping units and for all installed rotating equipment, such as engines, pumps, compressors, etc3.- Leads the implementation of Base Business initiative, SAP Maintenance Module to ensure successful implementation of a fully functional CMMS System. Effectiveness of planned maintenance program and coordinates work group’s efforts to drive maximum performance on reliability and operational excellence.4.- Actively promotes safety, efficiency, reliability, and waste minimization. Accountable for delivering business plan HSE targets. Fosters an Incident Injury Free Operations (IIF) environment using the Operational Excellence (OE) Management System.5.- Demonstrated troubleshooting capabilities and knowledge of facility equipment and systems.6.- Proven leadership skills, aligning and inspiring both company and contract personnel.7.- Strong communication skills and the ability to manage time effectively with minimal supervision.8.- Develops Root Cause Analysis (RCA’s) of rotating equipment and predictive/diagnostics analysis.
Preferred Qualifications:
Graduated as Mechanical, Maintenance Engineer with proven minimum of 15 years’ experience as maintenance engineer with emphasis on supporting operations and maintenance of Dehydration Plants, Flow Stations and Pumping Units and associated field and plant processing equipment.Oil & Gas experience is highly desired.
Chevron participates in E-Verify in certain locations as required by law.
Chevron Corporation is one of the world's leading integrated energy companies. Through its subsidiaries that conduct business worldwide, the company is involved in virtually every facet of the energy industry. Chevron explores for, produces and transports crude oil and natural gas; refines, markets and distributes transportation fuels and lubricants; manufactures and sells petrochemicals and additives; generates power; and develops and deploys technologies that enhance business value in every aspect of the company's operations. Chevron is based in San Ramon, Calif. More information about Chevron is available at www.chevron.com.
Chevron is an Equal Opportunity / Affirmative Action employer. Qualified applicants will receive consideration for employment without regard to race, color, religion, sex, sexual orientation, gender identity, national origin, disability or protected veteran status, or other status protected by law or regulation.
Chevron Corporation
-
- Chevron Corporation Jobs