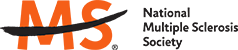
Job Information
Mars, Incorporated Red Process Lead in Lewisburg, Ohio
Job Description: Key Responsibilities
- Works directly with the Shift Manager to create the daily and weekly production plan, while focusing on associate capability and flawless execution.
- Ability to learn and perform all assigned activities & job tasks within line or area.
- As the key trainer and equipment/machinery expert of an assigned area, responsible to build operator capability, problem solving and technical understanding across teams and shifts.
- In the absence of the Shift Manager, performs the duties of the role demonstrating the necessary leadership behaviors.
- Is an integral part of Autonomous Maintenance (AM) and Daily Management Systems (DMS) managing guidance and training to Associates on MSE.
- Drives continuous improvement in the area to improve Key Performance Indicators (KPIs) such as safety, quality, productivity, and waste reduction.
- Participates in the execution of planned production "stops" to perform regular maintenance or other routine activities, coach operators on the effectiveness of proactive planning verses unplanned breakdowns.
- Influence and mentor associates on their self-development and business objectives.
- May relieve operators as needed within assigned production areas.
- Works Independently within established procedures and practices
Physical/Environmental Requirements:
- Standing on a concrete floor.
- Wearing proper personal protective equipment (bump cap, ear plugs, safety shoes, and uniform).
- Bending, stooping, twist, turn, standing for extended time periods, reaching, climbing stairs, and lifting up to 50 lbs.
- Forklift assignments require OSHA certification and getting on and off frequently.
- Available to work overtime daily based on needs of the business.
- Available to work overtime on weekends during peak season.
Context and Scope The Production Coordinator leads through the Mars 5 Principles and the Associate Concept. They seek to build their team to be able to succeed autonomously. They own all plant operations In their area, on their designated shift to ensure performance in a 24 hr day factory. Job Specifications/Qualifications Education & Professional Qualifications High School Diploma (or equivalent) & minimum of 3 years of experience in high-speed manufacturing, continuous improvement environment. Preferred:
- Associate Degree in a technical field of study and 2 years' experience in a TPM/technical, manufacturing environment or 5+ years of experience in manufacturing with progressive levels of responsibility
- Certified Trainer (Daily Management System (DMS) Autonomous Maintenance (AM), Problem solving, etc.)
Knowledge / Experience
- Required to learn all the skills and knowledge of Technician roles within their designated area.
- Has the ability to learn, operate, and knowledge to manage the operations of all the production equipment of multiple production areas within a factory.
- Complete all the necessary training and requirements to become a recognized Autonomous Maintenance Coach within the AM Pillar
- Maintain the ability to effectively train associates on their team.
- Has advanced skills, typically gained through a combination
- of job-related training and considerable work experience.
- Demonstrated experience in leading change and situational leadership.
- Effective written and oral communication skills.
- Proficient in MS Office (Excel to capture and analyze data and utilize PowerPoint to deliver presentations and training) and SAP.
Note: competencies selected should be job related
Drive For Results