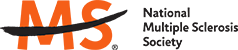
Job Information
GE Appliances, a Haier company 3rd Shift PLC Maintenance Technician in LaFayette, Georgia
At GE Appliances, a Haier company, we come together to make “good things, for life.” As the fastest-growing appliance company in the U.S., we’re powered by creators, thinkers and makers who believe that anything is possible and that there’s always a better way. We believe in the power of our people and in giving them the freedom to explore, discover and build good things, together.
The GE Appliances philosophy, backed by three simple commitments defines the way we work, invent, create, do business, and serve our communities: we come together , we always look for a better way , and we create possibilities .
Interested in joining us on our journey?
Join Roper Corporation team in a high-energy, production facility environment. Our Maintenance Technicians support appliance manufacturing operations to ensure equipment reliability and uptime in support of safety, quality, delivery, and cost objectives. It is an essential industrial maintenance role involving machine setup, troubleshooting, repair, and preventative maintenance to mechanical, electrical, pneumatic, and hydraulic equipment.
Responsible for reducing unscheduled maintenance, increasing uptime, and lowering maintenance costs by developing maintenance capabilities and effectiveness. Responsible for performing duties to install, troubleshoot, repair, and maintain production and facility equipment according to safety production and maintenance processes to support the achievement of the site's business goals and objectives.
This position is 3rd shift, 6:30pm-6:30am – D shift – 12 hour swing shift.
Weekends required.
Position
3rd Shift PLC Maintenance Technician
Location
USA, LaFayette, GA
How You'll Create Possibilities
Essential Duties and Responsibilities
Troubleshoot, install, repair and maintain the operating condition of industrial production and processing machinery and equipment, to include but not limited to: electrical systems (480), hydraulic and pneumatic systems, motors, gearboxes, VFD/HMI/Servo control devices, conveying systems, pumps, valves, photo eyes, switches, machine alignment, belt drives, chain drives, bearings, rollers, turn tables, flippers, manipulators, elevators, lowerators, heat exchangers, level controls.
Provide quick response to maintenance requests and calls from maintenance leadership and manufacturing operations teams
Ability to create advanced control systems and programs for process and operational control.
Possess basic understanding of ABB and Fanuc robots; Electrical system components – PLC’s, robotics, and other associated automation equipment.
Operate safely electrical test equipment
Troubleshoot and repair low voltage control circuits and three phase motor circuits up to 480 volts
Perform preventive maintenance on equipment
Assist in the installation of plant and process equipment
Provide corrective maintenance – including Root Cause Analysis
Effectively provide feedback/training to Operator Technicians as needed
Follow safe work methods and procedures to avoid injury to self and co-workers or damage to company property, including use of all required personal protective equipment, following safety precautions (e.g. LOTO), ensuring machine guards, etc.
Follow proper housekeeping standards to ensure clean and organized line maintenance work areas
Operate motorized equipment, including but not limited to scissor lifts, JLGs, fork trucks, etc.
Use a wide range of powered tools and hand tools and vibratory tools/equipment
Install new fixtures, motors, light and control circuits and other electrical equipment as required.
Work with PLC, including upload/download program, troubleshoot discrete ladder logic, forces, searching, and timers
Working knowledge of PLCs (modern Studio 5000 and legacy RsLogix 500 Allen Bradley SLC PLCs, Siemens), FANUC and ABB Robots, Cognex Vision Systems, VFDs, & HMI programming.
Critical Knowledge and Skills
Monitor and apply safety standards to maintain a safe working environment.
Ability to install, commission and troubleshoot automated industrial electrical-electronic controls and installations.
Provide PLC systems support, robotic applications, including PLC and HMI programming
Provide electrical-electronic support, including but not limited to, troubleshooting and component setup.
Provide mechanical support, including but not limited to, assembly, disassembly and rebuild of automated production equipment and systems.
Diagnoses and repairs or replaces faulty electronic components or logic.
Must be able to interact and communicate with internal customers. Internal customers may include manufacturing, engineers, project manager and management personnel.
Ability to prioritize workload and shift work activities in order to meet plant needs.
Tests malfunctioning machinery and determines technical issue and potential remedy.
Replaces faulty electrical components of machine such as relays, switches, and motors, and positions sensing devices. Reviews equipment schematics/manuals for specification concerning placement parts and installation.
Replaces electric motor bearings and rewires motors.
Diagnoses and replaces faulty mechanical, hydraulic, and pneumatic components of machines and equipment.
Periodically is scheduled for off-hours/emergency call-in to repair equipment or other technical related problems.
Responsible for promoting safety awareness and keeping safety as a number one priority on a daily basis.
Optimizes existing equipment capacity and anticipates utilization demands or equipment inhibitors.
Use of Hand Tools, Power Tools, and Diagnostic Tools; operate Fork-lifts and Man-lifts
Provides technical expertise directly or assists staff in troubleshooting systems and equipment.
Experience working with Human Machine Interfaces (HMIs), Analog and digital AC/DC drive systems, pneumatic/hydraulic systems
Possess experience working with 480V, 220V, 120V, and low volt DC electrical controls and systems and the ability to read and understand electrical, pneumatic, and hydraulic schematics
What You'll Bring to Our Team
Physical Demands
Ability to read and concentrate via computer data entry typing
Must be able to climb ladders and/or stairs and walk on open grating on elevated surfaces
Reasonable accommodations may be made to enable individuals with disabilities to perform the essential functions
Required to reach with hands and arms and stoop, kneel, or crouch
Perform work in a loud/noisy environment
Change shifts and work overtime and weekends, as required
Work with parts/equipment which may be hot, cold, and/or wet
Work outside in all weather conditions and work at heights
Use a wide range of powered tools and hand tools and vibratory tools/equipment
Frequent sitting, walking, and standing, and occasional climbing, stooping, kneeling, crouching, crawling, and balancing
Frequent use of eye, hand, and finger coordination enabling the use of office machinery
Oral and auditory capacity enabling interpersonal communication as well as communication through automated devices such as the telephone
Required to sit, stand, walk, and use hands to finger, handle or feel objects, tools, or controls
Specific vision abilities required by this job include close vision, peripheral vision, depth perception, and the ability to adjust focus
Must continuously have the ability to differentiate colors precisely
Prolonged standing, frequently handling various parts for assembly, frequent walking, reaching at waist level, pushing/pulling, grasping/squeezing, pinching
Have fine motor dexterity, neck flexion, and be able to use air tools
Be able to reach overhead, reach at shoulder level, reach at knee and floor level
Bending, stooping, squatting, crouching, kneeling, crawling, ladder/stair climbing, pivoting, twisting, neck extension/rotation, and using vibratory tools also required
Occasionally operate business machines
Handling and lifting of parts and/or equipment (minimum of 42 lbs. lifting/carrying and 25 lbf. pushing/pulling is required)
Qualification/Certifications/Education
Must have a high school diploma, GED or GED equivalent and
Associates Degree or equivalent in Electrical or Mechanical field; Industrial Systems Technology; Instrumentation and Controls Technician; Automation Engineering Technology
Technical Certificates: Advanced PLC and HMI Technician II Certificate; Mechatronics Specialist Certificate; Programmable Control Technician; Robotic Technician Certificate; ABB Robotics; Mechanical Maintenance Technician; Industrial Electrician;
Certified Journeyman with 2 or more years of experience in one of the following trades: Electrical or Mechanical.
Possess at least 2 years of current hands-on working experience.
Our Culture
At GE Appliances, creativity meets passion and conversations lead to exceptional outcomes and experiences. We respect and value the unique backgrounds and experiences that everyone brings to GE Appliances. We believe a diverse workplace, where everyone is included and people can be their true and authentic selves, fosters creativity and innovation. We know our differences are our greatest strength. The very best innovations across every function of a company come from diverse teams. Our commitment to ensuring a safe and inclusive workplace where everyone is valued allows employees to perform at their best, every day. Diversity at GE Appliances helps us achieve zero distance to our owners, innovate smartly and connect to the communities and customers we serve. We encourage and support the ideas, aspirations, and the wellbeing of everyone - our employees and our communities
GE Appliances is a trust-based organization. It is important we offer our employees the flexibility they need to do their best work while balancing the needs of the business and individuals. When you join GE Appliances, you will have the opportunity to work with your leader to create a flexible work arrangement that balances the needs of the individual, team, and organization.
GE Appliances is an Equal Opportunity Employer. Employment decisions are made without regard to race, color, religion, national or ethnic origin, sex, sexual orientation, gender identity or expression, age, disability, protected veteran status or other characteristics protected by law.
GE Appliances participates in E-Verify and will provide the federal government with your Form I-9 information to confirm that you are authorized to work in the U.S
If you are an individual with a disability and need assistance or an accommodation to use our website or to apply, please send an e-mail to ask.recruiting@geappliances.com
GE Appliances, a Haier company
-
- GE Appliances, a Haier company Jobs