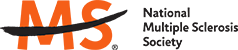
Job Information
Trane Technologies Supplier Quality Engineering Leader in La Crosse, Wisconsin
At Trane Technologies TM and through our businesses including Trane ® and Thermo King ® , we create innovative climate solutions for buildings, homes, and transportation that challenge what’s possible for a sustainable world. We're a team that dares to look at the world's challenges and see impactful possibilities. We believe in a better future when we uplift others and enable our people to thrive at work and at home. We boldly go.
Job Summary:
This position is responsible for the execution and optimization of the supplier quality system. This position will work cross functionally with Operations, Engineering and Quality to continuously improve supplier performance through the execution of various Supplier Quality Processes (i.e. SCAR, AUDIT, NCM, PPAP, and Supplier Monitoring). This will include ensuring compliance to the Global Supplier Quality Manual as defined in Trane Technologies Business Operating System (BOS).
Work Arrangement: This role will be located onsite at our La Crosse, WI facility with an expected annual travel of 15-20% and is considered safety-sensitive.
Thrive at work and at home:
· Benefits kick in on DAY ONE for you and your family, including health insurance and holistic wellness programs that include generous incentives – WE DARE TO CARE !
· Family building benefits include fertility coverage and adoption/surrogacy assistance.
· 401K match up to 6%, plus an additional 2% core contribution = up to 8% company contribution.
· Paid time off, including in support of volunteer and parental leave needs.
· Educational and training opportunities through company programs along with tuition assistance and student debt support .
· Learn more about our benefits here (https://careers.tranetechnologies.com/global/en/benefits) !
Responsibilities:
Responsible for product quality for the entire Supply Chain, from supplier to customer, of several Product Lines; drive effective root cause analysis to eliminate recurrence of non-conformances for all elements of the following:
• Supplier Quality - improve supplier quality by working with procurement, engineering, and suppliers. Enforce supplier chargeback process, capturing COPQ
• Provides suppliers with technical oversight and expertise in areas such as process development, PFMEA, control plans, PPAP, measurement systems, standard work, and error proofing when required.
• Ownership and management of the of SCAR's and follow-through activities of containment, root cause analysis, countermeasures, and verification of effectiveness by the supplier.
• Monitor, support and coordinate Supplier deviations (SDR). Take a leading role in defect analysis and continuous improvement efforts with goal of zero defects
• Management of supplier-caused quality escapes which may include on-site intervention.
• Manage supplier recovery initiatives as it relates to warranty, concessions, and production interruptions.
• Lead planning and approval of PPAPs collaborating with Quality and Engineering to help the supplier understand their objectives and our design requirements. Perform role of PPAP Coordinator.
• Lead Materials Review Board activity for components, coordinate activities between production, manufacturing, and manufacturing/design engineering. Responsible for material disposition. Lead containment activities, dispositions, RMA, and complete RTV for returning non-conforming material, MRB cage, and supplier chargeback/recovery process
• Regularly interface with both supplier and manufacturing to clarify and provide engineering input on supplier related issues (position requires coordination with MRB, Design Engineering, Leadership, support and shop personnel to resolve manufacturing and supplier problems)
• Leverage corporate supplier quality and supplier development team when needed.
• Establish and manage Receiving Inspection processes, as required.
• Drive continuous improvement for all elements of the Quality System.
• Know and comply with the Trane Quality Policy
• Work well with colleagues and produce results within a fast-paced and high-pressure atmosphere. Combine strong attention to detail with an orientation towards results/execution.
• Create, maintain, and report daily, weekly and/or monthly KPI
· Lead a team of 1 to 3 quality technicians to perform PPAPs
· Maintain KRONOS Pay System by reviewing, editing, and approving employee timecards
Key Competencies:
• We are seeking a high-energy Quality Engineer with a pragmatic problem-solving approach and compressed sense of time.
• Have a proven track record PPAP responsibility and addressing Quality issues with high visibility within an organization, a mindset of continuous improvement and a passion for root cause analysis.
• Requires a metric/results driven individual with a demonstrated experience in a Lean Manufacturing philosophy.
• Possess a strong understanding of effective Quality systems and methodologies and their impact on both the internal and external business environments; experience working in an ISO 9001 environment.
• Capable of using inspection tools (gages, optical comparator, CMM, etc.) and knowledgeable with manufacturing processes.
• Able to manage multiple initiatives simultaneously; able to engage members of Engineering, Sales, Purchasing or other teams as needed to address quality issues.
• Able to assist on the production floor as needed to ensure quality process compliance.
• Working knowledge of APQP, PPAP's, and First Article Submission.
• Proficiency with MSOffice Outlook, Excel, Word, Access, and PowerPoint.
Education/ Experience Requirements:
• Bachelor's degree in Engineering or related field required
• Previous manufacturing knowledge required.
• Proficient with Microsoft Office products
• ASQ Certified Quality Engineering certification preferred.
• Strong GD&T experience and knowledge with application of machined and fabricated parts.
• Knowledge of various quality system methodologies; CAR/8D, 5 Why's, Pareto Analysis, DFMEA, PFEMA, PPAP, APQP, etc. is a must.
• Knowledge of the ISO 9001:2015 Quality System preferred.
Compensation:
Base Pay Range: $90,000-$130,000.
Disclaimer: This base pay range is based on US national averages. Actual base pay could be a result of seniority, merit, geographic location where the work is performed.
Equal Employment Opportunity:
We offer competitive compensation and comprehensive benefits and programs. We are an equal opportunity employer; all qualified applicants will receive consideration for employment without regard to race, color, religion, sex, sexual orientation, gender identity, national origin, pregnancy, age, marital status, disability, status as a protected veteran, or any legally protected status.
Trane Technologies
-
- Trane Technologies Jobs