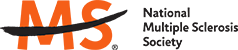
Job Information
Yulista Quality Engineer I (Manufacturing) JR105041 in Huntsville, Alabama
Quality Engineer (QE) will act as the functional group nonconforming material report/material review board owners and drive the resolution of Nonconformance Reports (NCR). QE will facilitate the Root Cause Corrective Action (RCCA) and Continuous Improvement (CI) processes for the functional areas based on internal audits and data-indicated problem areas. Support customer needs in functional areas using data analysis. This position is considered a quality leader. This is a hands-on role that interacts with assembly operators, quality inspectors, manufacturing, aviation, and engineering personnel to proactively ensure quality product that meet and/or exceed customer expectations.
ESSENTIAL FUNCTIONS
- Supports all Quality Management data, reports, analysis, etc. as directed by the Quality Manager.
- Ability to analyze and resolve design, manufacturing, and process issues varying from basic to very complex and technically challenging.
- Manages Material Review Boards to include disposition of non-conforming material, investigate/identify product containment, identify root cause and ensure corrective action is taken to prevent recurrence.
- Makes final MRB decision on product acceptability.
- Develops, modifies, applies, and maintains quality evaluation and control and protocols for processing materials into partially finished or finished materials product.
- Devises / implements methods and procedures for inspecting, testing, and evaluating the precision and accuracy of products and production equipment.
- Designs and analyzes inspection and testing processes, mechanisms, and equipment; conducts quality assurance tests; and performs statistical analysis to assess the cost of and determine the responsibility for, products or materials that do not meet required standards and specifications.
- Performs assessments / audits on processes and procedures to ensure compliance to specifications, engineering drawings, procedures and AS9100 / AS9110
- Attends program corrective action meetings, identifies trends, assists in problem resolution, and ensures responsible parties meet required standards through internal audits.
- Reviews documentation related to internal and external manufacturing processes to ensure quality products are delivered to the customer.
- Coordinate and expedite the flow of work and materials. Arrange for delivery, assembly or distribution of components and supplies to expedite flow of materials and meet production schedules.
- Performing mechanical/electrical drawing interpretation and problem resolution.
- Participate in continuous improvement initiatives and cross functional process development.
- Support planning, review, approval, and application of First Article Inspections (FAI)
- Professionally represents the organization in providing solutions to difficult technical issues associated with specific projects.
- Develops Standard Operating Procedures (SOP) and Work Instructions (WI) in support of organization needs.
- Provide technical expertise to company employees, suppliers, customers, and regulatory agencies to ensure compliance with contractual, company, and regulatory requirement.
- Other duties as directed by quality leadership.
SUPERVISORY RESPONSIBILITIES
The company evaluates performance, leadership skills, technical knowledge and individual achievements and these factors support the company in making decisions such as recommending personnel for promotions.
KNOWLEDGE, SKILLS, and ABILITIES:
- Knowledge with troubleshooting techniques and problem-solving skills
- Knowledge and application of LEAN and/or Six Sigma tools
- Working knowledge and experience with Deltek ERP tools, Microsoft Excel, Access, PowerPoint, SharePoint, and Word
- Excellent communication and presentation skills.
- Experience with use of inspection gages and measuring equipment.
- Prefer In-depth knowledge of Quality Engineering metho s, processes, and tools.
- Ability to identify a trend, conduct root cause analysis, and use quality principles/tools
- A strong background and experience in a manufacturing and/or aviation environment depending on organizational needs.
- AS9100/AS9110 experience preferred.
- AandP experience preferred.
QUALIFICATIONS:
- This position requires a Technical Engineering degree; with two (2) years experience; or associate degree with five (5) years experience or high school diploma with 10 years experience.
- Must be able to obtain and maintain a Government Security Clearance
- Certified Quality Engineer (CSQ) and / or Certified Quality Improvement Associate (CQIA) preferred
- Lean Six Sigma Certification (Green Belt / Black Belt) preferred
PREFERENCE STATEMENT Preference will be given to Calista shareholders and their descendants and to spouses of Calista shareholders, and to shareholders of other corporations created pursuant to the Alaska Native Claims Settlement Act, in accordance with Title 43 U.S. Code 1626(g).
EEO STATEMENT Additionally, it is our policy to select, place, train and promote the most qualified individuals based upon relevant factors such as work quality, attitude and experience, so as to provide equal employment opportunity for all employees in compliance with applicable local, state and federal laws and without regard to non-work related factors such as race, color, religion/creed, sex, national origin, age, disability, marital status, veteran status, pregnancy, sexual orientation, gender identity, citizenship, genetic information, or other protected status. When applicable, our policy of non-discrimination applies to all terms and conditions of employment, including but not limited to, recruiting, hiring, training, transfer, promotion, placement, layoff, compensation, termination, reduction in force and benefits.
REASONABLE ACCOMMODATION It is Calista and Subsidiaries' business philosophy and practice to provide reasonable accommodations, according to applicable state and federal laws, to all qualified individuals with physical or mental disabilities.
The statements contained in this job description are intended to describe the general content and requirements for performance of this job. It is not intended to be an exhaustive list of all job duties, responsibilities, and requirements.
This job description is not an employment agreement or contract. Management has the exclusive right to alter the scope of work within the framework of this job description at any time without prior notice.