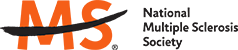
Job Information
System One Production Control Director (Aluminum) in Hubbard, Ohio
System One is looking for a Production Control Director for an aluminum casting client in Hubbard, Ohio.
Payrate: $120 - $150K
The Production Control Director (Aluminum) is responsible for directing, developing, and managing. the production planning and scheduling, inventory management, materials planning, warehousing, logistics, and purchasing activities related to operations.
The purpose of this position is to attain optimum scheduling of production lines to meet daily, weekly, and monthly order requirements; prepare and issue production and shipping schedules which will best utilize available capacities and staffing to provide prompt shipment and quality service to customers.
JOB QUALIFICATIONS
Must Have a Bachelor’s degree Industrial or Manufacturing Engineering. Graduate degree a plus
Minimum of 10 years’ experience in a manufacturing environment, aluminum manufacturing.
Strong computer skills including strong skill set with Windows, Excel, Word and Power Point.
Excellent communication skills both written and verbal and good organizational skills are also required.
Project management, problem solving and numerical/analytical skills a must.
Thorough understanding and application skill with statistical tools. Minitab experience a plus.
ESSENTIAL FUNCTIONS:
A Production Control Director in an aluminum casting manufacturing facility is responsible for overseeing the entire production process, ensuring efficient operations, high-quality output, and timely delivery. Essential functions that this role would typically involve:
Production Scheduling: Develop and maintain production schedules based on customer orders, inventory levels, and plant capacity.
Resource Planning: Allocate resources effectively, including raw materials, labor, and equipment, to meet production goals.
Inventory Management: Monitor and control inventory levels to ensure the right materials are available without overstocking. (RAW, WIP, and Finished Goods).
Process Optimization: Work closely with the General Manager and other Directors to continuously analyze and optimize manufacturing processes to improve efficiency and reduce waste..
Production Monitoring: Track production performance against schedules and targets, adjusting as necessary to avoid delays.
Workforce Management: Supervise and coordinate your team, ensuring proper training, development, and adherence to safety protocols.
Cost Control: Work closely with the financial and production teams to monitor production costs and identify areas for cost reduction without compromising quality or safety.
Supply Chain Coordination: Work closely with suppliers and procurement teams to ensure timely delivery of materials and parts.
Troubleshooting Production Issues: Address any production issues that arise, from equipment failures to bottlenecks in the production line.
Data Analysis and Reporting: Collect and analyze production data to prepare reports on performance, efficiency, and other key metrics. Maintain and present daily score cards.
Customer Communication: Communicate with customers to address production issues, delivery timelines, and any changes to orders or specifications.
Forecasting and Planning: Use historical data and trends to forecast future production needs, adjusting plans accordingly.
Risk Management: Identify potential risks to production schedules and take proactive measures to mitigate them.
Team Leadership and Motivation: Lead by example, fostering a positive and productive work environment while motivating staff to achieve production goals.
Continuous Improvement Initiatives: Lead efforts for continuous improvement through lean manufacturing practices and other process improvement strategies.
Problem Solving and Decision Making: Make decisions quickly and effectively when unexpected production challenges arise, balancing short-term fixes with long-term solutions.
ADDITIONAL RESPONSIBILITIES:
This position requires a flexible work schedule that may include extended work hours as predicated by production needs. Duties take place in an office environment with a significant amount of interaction with operations management. The position will act as a direct source of information on material status for manufacturing managers and supervision. Key Actions include expediting and monitoring of material flow to meet Master Production Schedule requirements (MPS), monitoring inventory levels for Work-In-Process (WIP) and raw material and alerting the factor support team on issues concerning holds or issues on materials.
#M1
System One is looking for a Production Control Director for an aluminum casting client in Hubbard, Ohio.
Payrate: $120 - $150K
The Production Control Director (Aluminum) is responsible for directing, developing, and managing. the production planning and scheduling, inventory management, materials planning, warehousing, logistics, and purchasing activities related to operations.
The purpose of this position is to attain optimum scheduling of production lines to meet daily, weekly, and monthly order requirements; prepare and issue production and shipping schedules which will best utilize available capacities and staffing to provide prompt shipment and quality service to customers.
JOB QUALIFICATIONS
Must Have a Bachelor’s degree Industrial or Manufacturing Engineering. Graduate degree a plus
Minimum of 10 years’ experience in a manufacturing environment, aluminum manufacturing.
Strong computer skills including strong skill set with Windows, Excel, Word and Power Point.
Excellent communication skills both written and verbal and good organizational skills are also required.
Project management, problem solving and numerical/analytical skills a must.
Thorough understanding and application skill with statistical tools. Minitab experience a plus.
ESSENTIAL FUNCTIONS:
A Production Control Director in an aluminum casting manufacturing facility is responsible for overseeing the entire production process, ensuring efficient operations, high-quality output, and timely delivery. Essential functions that this role would typically involve:
Production Scheduling: Develop and maintain production schedules based on customer orders, inventory levels, and plant capacity.
Resource Planning: Allocate resources effectively, including raw materials, labor, and equipment, to meet production goals.
Inventory Management: Monitor and control inventory levels to ensure the right materials are available without overstocking. (RAW, WIP, and Finished Goods).
Process Optimization: Work closely with the General Manager and other Directors to continuously analyze and optimize manufacturing processes to improve efficiency and reduce waste..
Production Monitoring: Track production performance against schedules and targets, adjusting as necessary to avoid delays.
Workforce Management: Supervise and coordinate your team, ensuring proper training, development, and adherence to safety protocols.
Cost Control: Work closely with the financial and production teams to monitor production costs and identify areas for cost reduction without compromising quality or safety.
Supply Chain Coordination: Work closely with suppliers and procurement teams to ensure timely delivery of materials and parts.
Troubleshooting Production Issues: Address any production issues that arise, from equipment failures to bottlenecks in the production line.
Data Analysis and Reporting: Collect and analyze production data to prepare reports on performance, efficiency, and other key metrics. Maintain and present daily score cards.
Customer Communication: Communicate with customers to address production issues, delivery timelines, and any changes to orders or specifications.
Forecasting and Planning: Use historical data and trends to forecast future production needs, adjusting plans accordingly.
Risk Management: Identify potential risks to production schedules and take proactive measures to mitigate them.
Team Leadership and Motivation: Lead by example, fostering a positive and productive work environment while motivating staff to achieve production goals.
Continuous Improvement Initiatives: Lead efforts for continuous improvement through lean manufacturing practices and other process improvement strategies.
Problem Solving and Decision Making: Make decisions quickly and effectively when unexpected production challenges arise, balancing short-term fixes with long-term solutions.
ADDITIONAL RESPONSIBILITIES:
This position requires a flexible work schedule that may include extended work hours as predicated by production needs. Duties take place in an office environment with a significant amount of interaction with operations management. The position will act as a direct source of information on material status for manufacturing managers and supervision. Key Actions include expediting and monitoring of material flow to meet Master Production Schedule requirements (MPS), monitoring inventory levels for Work-In-Process (WIP) and raw material and alerting the factor support team on issues concerning holds or issues on materials.
#M1
Ref: #404-IT Pittsburgh
Ref: #260-Eng NY Transit
System One, and its subsidiaries including Joulé, ALTA IT Services, CM Access, TPGS, and MOUNTAIN, LTD., are leaders in delivering workforce solutions and integrated services across North America. We help clients get work done more efficiently and economically, without compromising quality. System One not only serves as a valued partner for our clients, but we offer eligible full-time employees health and welfare benefits coverage options including medical, dental, vision, spending accounts, life insurance, voluntary plans, as well as participation in a 401(k) plan.
System One is an Equal Opportunity Employer. All qualified applicants will receive consideration for employment without regard to race, color, religion, sex (including pregnancy, childbirth, or related medical conditions), sexual orientation, gender identity, age, national origin, disability, family care or medical leave status, genetic information, veteran status, marital status, or any other characteristic protected by applicable federal, state, or local law.
System One
-
- System One Jobs