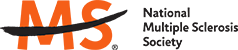
Job Information
RESILIENCE US INC Facilities Engineer III in Hamilton, Ohio
A career at Resilience is more than just a job - it's an opportunity to change the future. Resilience is a technology-focused biomanufacturing company that's changing the way medicine is made. We're building a sustainable network of high-tech, end-to-end manufacturing solutions to better withstand disruptive events, serve scientific discovery, and reach those in need. For more information, please visit www.resilience.com Position Summary & Responsibilities This position provides engineering support for GMP and non-GMP, utility systems, and related equipment. Coordinate the activities of third-party representatives. Manage the design, implementation, and support of site-wide process automation, supervisory control, and data acquisition (SCADA) solution. Provides Facilities support on Capital Projects. Understands and follows site specifications for all projects. Participate in new equipment design specification. Ensures good engineering and documentation practices are used during job activities. Conduct troubleshooting activities to support Facilities utilities and systems. Gather, organize, and communicate operational information to others. Lead and coordinate investigations and studies. Use CMMS (Computerized Maintenance Management System) to manage logistics. Identify temporary and permanent fixes to address issues. Initiate appropriate actions when process deviations occur. Mange and own change controls, corrective actions, impact assessments, change control action items, deviations, and periodic reviews. Monitor records to ensure compliance with regulatory requirements. Monitor equipment and/or systems for performance and problem indicators. Perform data entry. Read, understand, and comply with cGMP (Good Manufacturing Practices) and SOPs (Standard Operating Procedures), including general safety, lock outs, and so on. Wear gowning and PPE (Personal Protective Equipment) as required by specific activities. Maintain equipment and systems along with their certification records. Read and interpret diagrams, drawings, and other schematics. Support Facilities utilities and systems for issues or utilities improvements. Answer compliance and process questions from others. Communicate policies and procedures to employees. Establish visual tracking and other tools to enhance audit readiness and trend analysis. Lead process improvement activities and teams to meet strategic goals. Attend and facilitate team meetings to discuss progress, initiatives, and/or other matters. Guide others on SOPs (Standard Operating Procedures), control documents, and/or other work instructions. Coordinate activities of support groups. Analyze trends in data in order to provide accurate descriptions, identify root causes, and/or identify solutions or improvements. Monitor key performance indicators to meet strategic goals. Perform regular audits of SOPs (Standard Operating Procedures) and/or work instructions. Review and approve documentation needed for qualification of equipment and processes. Write, review, and revise SOPs (Standard Operating Procedures) for maintenance of equipment, systems, and/or facilities. Attend and facilitate inter-departmental meetings to discuss matters involving the coordination of multiple departments. Interact with other departments to implement corrective/preventative actions. Participate in cross-functional teams to meet strategic goals. Read technical publications and manuals and write associated procedures. Collect, record, and report metrics. Assess and implement improvements in productivity, waste generation, quality and cost. Provide input on the engineering of replacement parts. Assist process engineering and managers with improvement projects. Conduct presentations (other than training) for different audiences. Consult cross-functionally as an SME (Subject