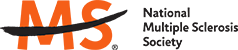
Job Information
O'Neal Industries, Inc. QA Manager - O'Neal Manufacturing Services in Greensboro, North Carolina
Description
Duties and Responsibilities
Learn, apply and promote the Vision, Mission, and Values of O’Neal Manufacturing Services.
Effectively communicate quality goals and objectives to plant personnel and lead achievement efforts.
Manage QA department activities to ensure that resources are effectively utilized and customer goals and deadlines are routinely met.
Develop and deploy development plans for QA personnel to ensure department is functioning at a high level.
Staff and equip the QA function for all critical quality functions including product inspection, metrology, auditing, process control, and continual improvement such that customer requirements and expectations are met.
Communicate effectively and proactively with customers to ensure problems are addressed and impact to OMS is mitigated.
Lead plant PPAP activities and coordinate with other plant staff to ensure seamless product launches.
Investigate root cause and implement permanent corrective actions for all customer complaints.
Respond to customer corrective action requests in a timely fashion and in the format required. (5-Why, 8-D etc.)
Ensure that corrective actions are initiated in MQ1, root causes are identified, and countermeasures are deployed and effective for internal and external quality issues.
Oversee the containment process when problems are encountered so as to mitigate the impact of the problem throughout the supply chain.
Conduct statistical capability studies on parts / processes and utilize the data to make process / equipment improvement recommendations.
Evaluate and implement measurement tools to assist in the production of a quality product.
Administer the company Layered Process Audit (LPA) program to drive improvement in product and process quality and overall customer satisfaction.
Write and implement work instructions to prevent the manufacture of defective products.
Identify and implement quality gates to prevent defects from being passed to the next process.
Skills and Qualifications
Must have or be pursuing a Bachelors or Associates degree in a related technical field or have equivalent related experience.
5 or more years of relevant quality experience working in a manufacturing environment.
Prior experience managing an ISO9001 based quality management system.
3 or more years’ experience supervising/managing people.
Experience working with automotive core tools (APQP, PPAP, FMEA, SPC, and MSA).
Familiarity with GD&T concepts and dimensional measurement techniques.
Experience working with OEM customers.
Experience with Lean Systems and / or 6-Sigma Green / Black Belt or similar structured problem-solving methodology.
Prior quality engineering experience strongly preferred.
Physical Requirements
Ability to lift 20 lbs. as needed.
Ability to bend, stand, climb, twist and stoop for extended periods of time.
Ability to perform sedentary work including sitting for extended periods of time.
Ability to operate standard office equipment.
Have good vision of 20/30 with corrective lenses.
Ability to maintain coordination of hand and finger movements to grasp and manipulate objects with precision.
Travel as needed to accomplish desired results. Overnight travel may be required occasionally.
Subject to environmental conditions that occur indoors and outdoors which includes but is not limited to exposure to changing temperatures, loud noises, vibration from use of equipment and the following:
Hazards: Variety of physical conditions, such as proximity to moving mechanical parts, electrical current, exposure to high heat or exposure to chemicals.
Atmospheric conditions: One or more of the following conditions that affect the respiratory system or the skin – fumes, odors, dust, mist, gases or poor ventilation.
Oils: there is air and/or skin exposure to oils and other cutting fluids.
Benefits
Medical, Dental, and Vision Insurance
401k with Company Match
Paid Time Off
Paid Holidays
Paid Community Service Day
Company Paid Life Insurance
Company Paid Short-Term Disability
Company Paid Long-Term Disability
Tuition Reimbursement
Wellness Programs
Employee Assistance Program
About Us
At O’Neal Manufacturing Services (OMS), we build things! As an O’Neal Industries affiliate company, we are a leader in the fabrication of steel and metal products that shape the world in which we live in. Our culture is driven by honesty, integrity and respect. We set high expectations for ourselves in providing a safe and diverse work environment. If you are looking to be part of a dynamic company to build your career, visit onealmfg.com/careers to learn more!
OMS Greensboro is known as the manufacturing center of North Carolina for over 50 years. Greensboro is home to a 226,000 sq. ft. O’Neal Manufacturing Services (OMS) production facility. Our Greensboro, NC facility offers advanced manufacturing equipment and an experienced staff to support multi-step metal fabrication for many customers in the construction and heavy equipment industries. OMS Greensboro is ISO 9001: 2015 certified and is your “one-stop shop” supply chain solution, delivering high-quality fabrications on-time and at an affordable price.
Equal Opportunity Employer/Protected Veterans/Individuals with Disabilities
The contractor will not discharge or in any other manner discriminate against employees or applicants because they have inquired about, discussed, or disclosed their own pay or the pay of another employee or applicant. However, employees who have access to the compensation information of other employees or applicants as a part of their essential job functions cannot disclose the pay of other employees or applicants to individuals who do not otherwise have access to compensation information, unless the disclosure is (a) in response to a formal complaint or charge, (b) in furtherance of an investigation, proceeding, hearing, or action, including an investigation conducted by the employer, or (c) consistent with the contractor’s legal duty to furnish information. 41 CFR 60-1.35(c)
O'Neal Industries, Inc.
-
- O'Neal Industries, Inc. Jobs