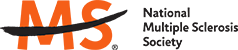
Job Information
DuPont Sr. Process Engineer in Fayetteville, North Carolina
At DuPont, we are working on things that matter; whether it’s providing clean water to more than a billion people on the planet, producing materials that are essential in everyday technology devices from smartphones to electric vehicles, or protecting workers around the world.
If you would like to be a part of a premier multi-industrial company that is delivering sustainable solutions that bring real purpose and value, of a company with collaborative spirit because it believes that we work best when we work together as a team and values the diversity of thought, then DuPont is the company for you!
WHY JOIN US?
Our purpose is to empower the world with essential innovations to thrive. We work on things that matter!
Have the Opportunity to chart your own course, challenge yourself, and acquire new capabilities to build a rewarding and fulfilling career. We reward employees with competitive pay and incentives to recognize skills, competencies, and contributions to business results.
Get to Experience a collaborative environment where teamwork is celebrated with flexibility that enhances balance and an inclusive atmosphere that is welcoming to all!
Get to know our Purpose and make it yours by bringing innovations to market that improve the world, share a commitment to sustainability that makes our planet better and give back to communities in which we work and live.
DuPont Electronics and Imaging Business has an opening for a Production Engineer located in Fayetteville, NC site.
The successful candidate will provide day-to-day technical support to the Vinyl Fluoride Operation by applying technical skills to optimize plant operations, resolve plant problems, and enable safe and efficient production of low cost, quality products.
Your Key Responsibilities:
Apply knowledge of their plant and technology – study historical data, convene with Tech Center or other SMEs, etc. Earn respect and trust of operations team through excellent problem-solving skills and technical expertise.
Utilize defined Most Effective Technology and challenge/escalate MET application and assumptions when better solutions arise.
Ensure Process Automation is effectively utilized to optimize plant performance.
Partner with the experts to perform advanced troubleshooting and improve operating discipline. Diagnose and document root causes of asset utilization losses in the facility.
Understand why specific procedure steps and precautions are needed and keep a strong field presence to reinforce the importance.
Conduct daily review of logbook and alarm history to better understand the plant operation and stay engaged with daily activities. Maintain, own, and review daily KPIs/ trends to ensure optimum performance.
Respond urgently to plant issues and emergencies. Act as a unit technical expert during unplanned events and drive implementation of effective corrective and preventative actions.
Provide leadership, expertise, diagnosis, and optimization in plant Raw Material Efficiency, which may include yield or waste generation.
Ensure compliance with plant operating permits.
Understand site integration and provide input to optimize the overall system.
Learn and apply continuous improvement, value creation, and financial acumen skills to accelerate profitability and low-cost service of the facility.
Drive high levels of quality, responsiveness, and reliability for the customer.
Actively work to maximize plant margin by understanding how much the plant makes per day and based on the product slate. Set up metrics and management systems to optimize the cost position and EBITDA generation of the plant.
Pass certification of technical skills, technology, and process safety expertise.
Mentor other technical staff members and operators as appropriate in process fundamentals, plant technology, and application of process safety
Conducts work activities and demonstrates leadership behavior consistent with DuPont Core Values
Takes ownership of process performance metrics of safety, production rate, yield and uptime.
Serves as first response to area technical issues and assists in troubleshooting process or equipment issues. Leads teams in root cause analysis and problem solving.
Participates as part of a team to upgrade products and processes by designing and implementing capital and cost equipment upgrades, developing, and executing test authorizations and improving control strategies.
Actively participates in strengthening PSM performance and compliance including leading PSM elements as needed.
Helps to train personnel and build technical capability of work teams.
Qualifications:
BS Chemical Engineering Degree required.
5+ years of manufacturing or related experience required.
Process Safety Management (High Hazard Process/Low Hazard Operation) experience preferred.
Effective communication skills
Project Management Expertise (Global Product Methodology)
Six Sigma Certification (preferred)
Join our Talent Community (http://careers.dupont.com/us/en/jointalentcommunity) to stay connected with us!
DuPont is an equal opportunity employer. Qualified applicants will be considered without regard to race, color, religion, creed, sex, sexual orientation, gender identity, marital status, national origin, age, veteran status, disability or any other protected class. If you need a reasonable accommodation to search or apply for a position, please visit our Accessibility Page for Contact Information (http://www.dupont.com/global-links/accessibility.html) .
DuPont
-
- DuPont Jobs