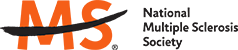
Job Information
ABM Industries Senior Coordinator in Ellicott City, Maryland
The Critical Environment Operations Coordinator is responsible for the effective execution of all maintenance work controls processes. The primary role is to improve work force productivity and work quality by anticipating and eliminating potential delays through planning and coordination (scheduling) of labor, parts and material, tools external services, rentals, equipment, required permits, specialized documentation and equipment access. This position is empowered to manage work priority, develop job plans, define parts and materials, define crafts and skills, and engage the proper resources to develop a safe, effective, and efficient work control plan.
Pay: $65,000-$90,000
The pay listed is the salary range for this position. Any specific offer will vary based on the successful applicant’s education, experience, skills, abilities, geographic location, and alignment with market data.
You may be eligible to participate in a Company incentive or bonus program.
Benefit Information:
ABM offers a comprehensive benefits package. For information about ABM’s benefits, visit ABM 2025 Employee Benefits | Staff & Management
ESSENTIAL DUTIES AND RESPONSIBILITIES
This position coordinates with our operations and maintenance management team in developing the scheduled maintenance activities and processes; pre-evaluates the need for replacement parts and places orders; and anticipates interruptions in plan and develops backup plans to minimize the impact on the facility’s overall functionality or production schedule. This position is the principal liaison between the maintenance department and operation planning.
Maintains CMMS while managing and tracking work orders, backlog, and spare parts and creates a machine history of plant equipment and reallocates resources as required.
Initiates the requisition process for all MRO materials and oversees storeroom to establish, maintain, improve, and optimize MRO inventory.
Plans/Schedules work activities for critical environment staff. Develops maintenance work schedule for affected area including preventative and predictive maintenance and develops and adheres to prioritization of work tasks.
Maintains accurate metrics on the performance of planning/scheduling functions and provides information for continuous improvement. Maximizes equipment reliability and availability through effective use of planned maintenance.
Develops a system of planned job packages for recurring tasks.
Coordinates work with third party vendors. Review’s subcontractor paperwork including reports and other related documentation.
Ensures all maintenance personnel understand the work instructions using a procedures-based maintenance strategy/best practices for all maintenance tasks and update and close each work order when completed.
Receives and reviews all planned work orders to verify proper completion with all required information; examines planned work orders and determines scope and best practices to accomplish work; analyzes unplanned work orders and occurrences for incorporation into corrective and preventive actions; and performs post job reviews to ensure actual work performed and post repair operation is satisfactory.
Initiates, implements, and develops full scope and extent of work required, including cost and time required, to plan/schedule/conduct the relevant repair, preventive, predictive, and improvement maintenance activities of the plant equipment, buildings, and grounds.
Identifies/secures/replaces all parts and material required to complete the work by providing stores a bill of material for the work orders and kits (palletizes). planning and scheduling flow and process tasks.
Identifies work requiring engineering and design and reviews with proper entities.
Prepares job plans for scheduling, detailing parts, materials, special tools and external services and documentation with planned costs; and performs root cause analysis.
Prepares reports, collects, and analyzes data, and makes recommendations for improving operations and solving maintenance/operation related problems.
Understands the as-designed operation of all plant assets and reviews the operation of equipment and systems to identify and implement PM and PDM tasks to avoid production interruption.
Creates a critical spares list and procures or identifies sources for procurement to reduce lead times.
Other duties as assigned by Management.
EXPERIENCE AND EDUCATION AND EQUIVALENT EXPERIENCE
Bachelor's degree in facility management, business administration, engineering, or related technical field, or demonstrated equivalent combination of education and experience, or 8 years of experience in industrial Facilities Maintenance related work will be considered demonstrated equivalent in experience with no college education.
Have an active US Government Top Secret Security Clearance
Proficiency utilizing a CMMS such as WebTMA, Alliance or Maximo.
Working knowledge of purchasing and/or utilizing and managing subcontracts and vendors
Excellent project/program management skills, ability to work in fast-paced work environment, ability to prioritize tasks effectively, and an ability to work effectively across organizational boundaries.
Understanding and implementation of risk mitigation processes.
PHYSICAL DEMANDS AND WORK ENVIRONMENTAL FACTORS
The position requires frequent prolonged sitting in an office environment. The employee will be frequently required to turn head and torso, bend and flex arms, wrists, and fingers, reach with hands and arms, lift or move objects weighing 10 lbs. or more. Position requires that employee have full use of eyes and ears and full power of speech.
ABM Industries
-
- ABM Industries Jobs