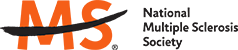
Job Information
Talen Energy Lead O & M Technician in Dartmouth, Massachusetts
Primary Purpose & Summary:
Under limited supervision and using considerable latitude for independent judgment, the Lead O&M Technician will demonstrate a thorough understanding and knowledge of operations and maintenance to the plant in order to maintain operate, and monitor all plant generating equipment/systems. Including responding to alarms by taking appropriate corrective actions and execute plant shutdown and start up procedures as required. Also, the Lead O&M Tech. will assure that the plant meets its generating requirements while operating and maintaining it in a safe and efficient manner. Additional areas of general knowledge and/or expertise may include, depending upon job responsibilities, an aptitude in instrumentation, controls, and electrical systems.
Responsibilities:
Supervise the operation of the combined cycle plant. Coordinate operations with the O&M Manager and ISO-NE and Eversource Electric Company while maintaining safe, efficient and reliable operation of the plant.
Maintain a thorough knowledge of all plant systems, operating and emergency response procedures and the ability to execute procedures and equipment when necessary and access the appropriate plant manuals.
Maintain a thorough knowledge of plant environmental emission parameters.
Investigate and clear all alarms by taking appropriate actions.
Perform plant start-up, shut-down and equipment operations as necessary, including the turbines, HRSG, and all auxiliary equipment in accordance with operating instructions and procedures.
Receive and respond to electrical, steam and fuel dispatcher's orders and requests.
Update maintain and review required plant logs and records on a continuous basis, precisely and accurately.
Control, monitor, record and chart plant performance and variances via computerized monitoring programs and other plant instrumentation.
Report upset conditions or other anomalies in plant status to the Facility Manager in a timely manner.
Identify and diagnose process problems and adjust/correct within skill capabilities.
Monitor and test water chemistry per written guidelines to maintain proper steam quality and boiler chemistry.
Assist in the training of new operators as required and, in the training, and development of plant operators.
Successfully complete company sponsored training courses and training and qualification programs as required. Ensure plant and equipment is maintained in a neat and orderly manner.
Safely operate plant equipment including trucks, cranes, forklifts and direct unloading of off-hour deliveries.
Monitor plant security utilizing systems provided.
Ensure accuracy of submitted defective equipment reports.
Ensure all personnel within the plant adhere to safety guidelines.
Insure proper "Lock-out/Tag-out" procedures are followed. Monitor status.
Support maintenance and operations activities as required, including assisting in the testing and maintenance of systems and equipment.
Make use of the plant preventive maintenance program by processing and completing work orders to ensure the upkeep and continued good performance of all plant equipment.
Will involve occasional work with OSHA classified hazardous materials.
May be required to work overtime in the form of additional hours per day and additional days per week as dictated by plant operations - including but not limited to call-in' s; vacations; outages (forced, & scheduled)
Skills/Competencies:
Ability to work in a complex, high pressure, production-oriented environment.
Ability to work and communicate effectively with all plant personnel as well as client and other outside representatives.
Ability to encounter new and varied work situations sometimes extremely complex in nature.
Ability to perform duties independently with only general direction.
Physical requirements include but are not limited to: ability to lift (50) pounds, use hand tools and test instruments, working on feet for 12 hour periods, requiring extensive stair and ladder climbing. Wearing of personal protective equipment in the performance of duties (e.g. hard hats, safety glasses, air masks, ear protection, chemical suits, etc.).
Position requires working varied rotating shifts including weekend and holiday coverage. "On Call" status may be required.
Ability to read one line engineering drawings.
Ability to distinguish between colors
Education & Experience:
Six years’ experience in operations and/or maintenance of major power plant equipment.
Experience with analog and digital control systems, plant IT platforms, and plant electrical distribution power systems.
Licenses/Certifications:
Valid Driver's License
Possess a MA Dept., of Public Safety Second Class Engineers License. ISO-NE SROT Certification.
Note: The statements contained in this job description are not necessarily all inclusive; additional duties may be assigned and requirements may vary from time to time.
Physical and Mental Demands:
The physical and mental demands identified below are representative of those that must be met by an employee to successfully perform the essential functions of the job. Reasonable accommodations may be made to enable individuals with disabilities to perform the essential functions.
Physical Demands:
Power Plant facility work requires tasks be performed in both in/out door environments, must be able to work in adverse conditions that may include, but not be limited to the following:
May be exposed to hazards associated with power and hand tools, dust, fumes, high pressure steam, high temperatures and confined spaces; and may be regularly subject to external environmental conditions such as cold, heat dust, snow or noise and fumes from equipment or chemicals.
While performing the duties of the job, the employee is regularly required to climb stairs, ladders, and work on elevated platforms including the stack. Must be able to stand for long periods of time, operate objects, tools or controls and reach with hands and arms. Must be willing to tolerate awkward and stretched positions while stooping, crouching, or kneeling to perform daily duties.
Must be able to lift 45 pounds overhead and 75 pounds from the floor to 36 inches.
Must be willing to travel to other facilities if needed.
Specific vision abilities required by this job include close vision, distance vision, color distinction with vision, peripheral vision, depth perception and the ability to adjust focus.
Noise levels are moderately loud and may vary in various areas of the plant site.
Must be able to work around high voltage.
Must have manual dexterity and ability to manipulate keyboards.
Must be capable of wearing respirators and working in dusty environments.
Mental Demands:
While performing the duties of the job, the employee is regularly required to use written and oral communication skills, read and interpret data, information and documents; analyze and solve complex problems, observe and interpret situations, use math and mathematical reasoning; deal with changing, intensive deadlines, and interact with internal and external clients. Must be able to concentrate while under time constraints.
Work Environment:
The employee is regularly exposed to outside weather conditions and wet or humid conditions. The employee regularly works near moving mechanical parts and may be exposed to toxic or caustic chemicals, fumes or airborne particles, potential risk of electrical shock and vibration.
Note: You will have an opportunity to add attachments to your application. Please use this opportunity to upload your resume, cover letter, and any relevant documents .
Talen owns and operates approximately 10.7 GW of power infrastructure in the United States. We produce and sell electricity, capacity, and ancillary services into wholesale power markets in the United States primarily in PJM and WECC, with our generation fleet principally located in the Mid-Atlantic and Montana.
We focus on excellence through safe and efficient operations. We have an inclusive, diverse, respectful, and collaborative workplace, and a strong commitment to innovation, teamwork, and integrity. Talen is headquartered in Houston, Texas.
Talen Energy is an equal opportunity employer dedicated to diversity and the strength it brings to the workplace. All qualified applicants will receive consideration for employment without regard to race, color, age, sex, religion, national origin, veteran status, sexual orientation, genetic information, gender identity, disability, perceived disability, or any other protected characteristic as may be defined by applicable law.
For more information visit www.talenenergy.com .
If you need assistance with the application process, please email us at TalenEnergyRecruitment@talenenergy.com
Talen Energy
-
- Talen Energy Jobs