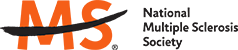
Job Information
Morton Salt Inc Manager, Production in Cape Canaveral, Florida
Manager, Production
Knowledge, Skills, and Abilities
- Bachelor's degree in engineering or a related technical field.
- Minimum of 5 - 8 years of experience in manufacturing, with a focus on plant operations.
- At least 5 years of experience in a leadership or managerial role within a manufacturing environment.
- Leadership: lead and motivate a diverse team of employees to achieve operational excellence and meet production targets.
- Operational Management: Proven experience in managing day-to-day plant operations, including production, maintenance, quality control, and safety.
- Problem-Solving: Skill in identifying operational challenges, analyzing root causes, and implementing solutions to improve plant performance.
- Strategic Thinking: align plant operations with overall business objectives and contribute to strategic planning initiatives.
- Communication: communication skills to convey goals, expectations, and operational updates to internal teams and senior management.
- Financial Acumen: Understanding of budgeting, cost control, and financial analysis to optimize plant performance and ensure profitability.
- Continuous Improvement: Commitment to driving continuous improvement initiatives to enhance plant efficiency, productivity, and quality.
- Safety and Compliance: Knowledge of health, safety, and environmental regulations, with a focus on ensuring compliance and maintaining a safe work environment.
- Team Building: foster a collaborative and culture within the plant, promoting teamwork, employee engagement, and morale.
- Decision-Making: make decisions, considering both short-term and long-term implications.
- Adaptability: Flexibility to adapt to changing business conditions, priorities, and operational challenges.
- Relationship Management: Skill in building and maintaining relationships with internal teams, external partners, and key stakeholders.
- To perform this job successfully, an individual should have computer skills, including spreadsheet and word processing software.
Job Summary
As the Production Manager, this role will be responsible for overseeing the Processing, Packaging, and Shipping Departments, ensuring operations in compliance with all Company Safety Management Systems and government regulations. This role's leadership will be crucial in delivering products to our customers while maintaining work environment.
Duties and Responsibilities:
- Safety Compliance: Ensure the safety of the plant environment by maintaining compliance with Company Policy and government regulations. Stay abreast of the Company's safety and health policies and OSHA regulations and implement measures to eliminate or minimize incidents.
- Employee Training and Compliance: Ensure all employees and contractors receive training and are fully aware and compliant with safety rules and regulations.
- Operational Oversight: Oversee processing, packaging, and shipping operations to meet production requirements and quality standards (FSQR, HACCP). Schedule shifts and hours of operation to maintain finished goods inventory levels and meet customer demand.
- Facility Maintenance: Develop timelines for biannual facility shutdowns and routine maintenance schedules. Monitor maintenance activities to ensure timely completion and minimize downtime.
- Budget Management: Responsible for budget compliance in the processing, packaging, and shipping departments. This includes preparing and submitting requisitions for new equipment and repair parts. Participate in Capital Appropriation Requests and recommend procurement of preferred equipment vendors and contractors.
- Project Management: Manage minor projects to ensure cost and timing targets are met. Participate in RFQs to provide detail, so bidders understand the scope of work and safety requirements. Utilize tracking tools to mon tor project milestones.
- Leadership and Employee Development: Lead department activities related to safety, incident investigation, and employee relations. Engage the workforce, outline clear roles and responsibilities, and incorporate performance management and employee development within the facility.
- Contractor Management: Select and monitor contractors to ensure compliance with government regulations and Company Policy.
- Performance Monitoring: Ensure department goals align with plant business objectives and monitor production lines to meet monthly budgeted targets.
- Maintenance Coordination: Collaborate with maintenance to determine routine timelines for department/equipment preventive maintenance, predictive maintenance, and repairs as needed.
- Continuous Improvement: Embrace continuous improvement initiatives to enhance efficiency and product quality. Monitor performance data on operations and recommend changes where beneficial.
- Product Quality Assurance: Provide leadership to drive continuous improvements in product quality. Communicate any issues regarding product safety, legality, or quality to the General Manager and Quality Supervisor.
- Training Documentation: Ensure documented training on all departmental Job Safety Analyses (JSAs) and Standard Operating Procedures (SOPs). Conduct a full SOP review every three years to maintain compliance and effectiveness.
- Recruitment and Selection: Requisition, screen, and select new employees using recruiting resources to maintain a skilled and qualified workforce.
- General Manager Backup: Serve as a backup for the General Manager as needed, providing support and continuity in their absence.
- Other Duties: Undertake any other duties as required to support plant operations and achieve organizational goals.
```{=html}
```
```{=html}
```
Physical Demands
The physical demands described here are representative of those that must be met by an employee to perform the essential functions of this job successfully. Reasonable accommodations may be made to enable individuals with disabilities to perform the essential functions.
While performing the duties of this Job, the employee is regularly required to talk or hear. The employee is frequently required to stand. The employee is occasionally required to walk, sit, use hands to finger, handle, or feel; reach with hands and arms; climb or balance; stoop, kneel, crouch, or crawl; and taste or smell. The employee must occasionally lift and/or move up to 50 pounds. Specific vision abilities required by this job include close vision, distance vision, color vision, peripheral vision, depth perception, and the ability to adjust focus.
Work Environment
The work environment characteristics described here are representative of those an employee encounters while performing the essential functions of this job. Reasonable accommodations may be made to enable individuals with disabilities to perform the essential functions.
While performing the duties of this Job, the employee is frequently exposed to moving mechanical parts. The employee is occasionally exposed to wet and/or humid conditions; high, precarious places; fumes or airborne particles; toxic or caustic chemicals; outside weather conditions; risk of ele