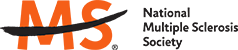
Job Information
Morton Salt Inc General Manager in Cape Canaveral, Florida
General Manager
Knowledge, Skills, and Abilities
- Bachelor's Degree in Engineering or other related technical degree.
- Minimum of 10 years of manufacturing experience, including a minimum of five (5) years in Production, Technical, or Maintenance management roles.
- Minimum of five (5) years of management experience is preferred.
- Leadership skills, inclusion, cooperation, and responsibility (RICR). Inspire and motivate teams towards achieving common goals.
- Lead and manage organizational change
- Resolve conflicts and negotiate solutions.
- Analytical skills; interpreting data and making data-driven decisions.
- Flexibility to adapt to changing business environments and priorities.
- Identify and implement innovative solutions to improve processes and drive efficiency.
- Works under high-pressure situations.
- Knowledge of risk assessment and mitigation strategies to ensure business continuity.
Physical Demands
- Works in seated or standing positions for prolonged periods of time, performs office or clerical duties, including the use of office tools, travels between office and plant environments of varied temperatures and humidity, climbs stairs, and wears personal protective equipment, as required.
- Works in a general office and manufacturing plant environment.
Job Summary
As the General Manager, this role will oversee and coordinate all aspects of facility operations to ensure optimal performance and profitability. This role will implement strategic directives to enhance the facility's competitive position and achieve business goals. Leading a team of supervisors and managers, this role will direct plans to control safety, environmental compliance, production outputs, CAPEX and operational budgets, labor efficiency, engineering effectiveness, facility maintenance and reliability, warehousing management, labor relations, and employee utilization. Through delegation and leadership, the individual will drive efficient and economical operations, aligning with the organization's objectives for profit, growth, and return on investment.
Duties and Responsibilities
- Compliance and Safety: Ensure compliance with OSHA and company EHS (Environmental, Health, and Safety) regulations. Continuously improve safety measures to provide a safe work environment for all employees.
- Quality and Environmental Standards: Maintain adherence to company Quality and Environmental standards, ensuring product safety, legality, and quality systems.
- Budget Management: Develop and manage the annual operating and capital budgets. Monitor and control CAPEX and operational spending, preparing monthly and year-to-date analyses comparing actual performance against budget.
- Production Management: Oversee all production operations to meet demand, maintain reliability, and ensure facility and equipment are in optimal condition.
- Resource Allocation: Strategically allocate resources to achieve plant goals and objectives. Maintain adequate inventory levels to ensure continuous production and finished goods.
- Engineering and Maintenance: Drive improvements in plant productivity through engineering changes and effective facility/equipment maintenance and reliability.
- Labor Efficiency and Workforce Development: Schedule labor levels to meet production and shipping plans, utilizing temporary personnel during peak periods. Develop the workforce for succession planning and ensure utilization of employees.
- Performance Management: Oversee performance management for direct reports and the entire site. Formulate and implement manufacturing strategies that align with company and local objectives.
- Communication and Relations: Foster and maintain relations with salaried and bargaining unit employees. Conduct regular meetings to ensure communication across the plant.
- Inventory and Supply Chain Management: Develop and review inventory control systems for bulk, package, and raw materials. Plan delivery of raw materials, including bags, pallet covers, slip sheets, additives, labels, and third-party purchased products.
- Security and Unloading Operations: Ensure site security is maintained at all times. Manage all aspects of vessel unloading, coordinating schedules and personnel for transfer of inbound products.
- Policy Compliance: Ensure all employees understand and comply with company policies and procedures.
- Deputy Management: Ensure the Production Manager is fully briefed and prepared to assume Facility Manager responsibilities in the latter's absence, acting as the designated deputy for Quality systems.
Health, Safety and Environmental
- Ensure compliance with all relevant health, safety, and environmental regulations, as well as corporate standards and policies.
- Manage EHS Performance: Oversee and manage the performance of health, safety, and environmental initiatives, aiming for continuous improvement and best practices.
- Promoting a culture of health, safety, and environmental stewardship throughout the organization.
Operational Performance
- Alignment with Business Imperatives: Ensure that department goals are aligned with the overarching business imperatives of the plant.
- Achievement of Performance Goals: Set and meet performance goals to drive operational excellence.
- Key Performance Indicators (KPIs): Establish and ensure the achievement of all unit-specific KPIs.
- Corporate Standards and Policy Compliance: Ensure compliance with corporate standards, including financial protocols and the code of business conduct, and adhere to all company policies.
- Budget and Cost Management: Manage the facility's budget, overseeing product costs, volume, and quality to optimize financial performance.
- Support for Business Processes: Support and enhance business processes to meet operational requirements.
People Management/Development
Promote Open Communication: Foster an environment where open communication is encouraged and valued.
Team Building: Cultivate a collaborative culture that emphasizes teamwork and collective success.
Problem-Solving and Continuous Improvement: Encourage a culture focused on innovative problem-solving and continuous process improvement.
Empower Decision-Making: Ensure that decision-making authority is delegated to the proper levels within the organization.
Clarify Roles and Responsibilities: Clearly define roles and responsibilities to ensure accountability and efficiency.
Workforce Engagement: engage the workforce to promote involvement and commitment.
Maintain Positive Morale: Strive to maintain high employee morale through recognition, support, and a positive work environment.
Resource Planning and Deployment: Develop and implement resource planning and deployment strategies.
Recruitment and Staffing: Conduct recruiting and staffing activities as necessary to meet operational needs.
Performance Management and Development: Facilitate performance management processes and support