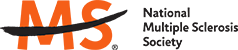
Job Information
Magna Industrial Engineer - Materials in Bowling Green, Kentucky
Industrial Engineer - Materials
Job Number: 67211
Group: Cosma International
Division: Bowling Green Metalforming
Job Type: Permanent/Regular
Location:
Bowling Green, KENTUCKY, US, 42103
Work Style:
Job Number: 67211
Group: Cosma International
Division : Bowling Green Metalforming
Job Type: Permanent/Regular
Location: BOWLING GREEN
Work Style:
About us
We see a future where everyone can live and move without limitations. That’s why we are developing technologies, systems and concepts that make vehicles safer and cleaner, while serving our communities, the planet and, above all, people.
Forward. For all.
Group Summary
Cosma provides a comprehensive range of body, chassis and engineering solutions to global customers. Through our robust product engineering, outstanding tooling capabilities and diverse process expertise, we continue to bring lightweight and innovative products to market.
About the Role
The Industrial Engineer is responsible to ensure that the Customer, People, and Investor goals are balanced and met.
The Industrial Engineer (IE) designs, develops, tests, evaluates, and implements integrated systems for managing industrial processes including human work factors, inventory control, logistics and material flow, cost analysis, and production coordination.
Your Responsibilities
Develop and maintain a plan for every part (PFEP).
Use the PFEP to support other BGM departments in planning for SOP, EOP, insourcing, outsourcing, etc.
Use the PFEP, facility layout, best practices/benchmarks, and Lean Manufacturing tools (ex: Value Stream Mapping, Kaizen, etc.) to identify and drive material flow improvements.
Provide information from the PFEP (packaging requirements, space requirements, delivery frequency, etc.) to other BGM Departments as requested.
Lead process improvement, cost savings, and cost avoidance projects involving resources and getting buy-in/approval from other departments within BGM.
Analyze data including customer requirements, operation sequence, material flow, functional statements, packaging requirements, cycle times, project information, etc. to determine/improve worker functions and responsibilities (work instruction) with the goal of efficient material flow and cost savings.
Evaluate and recommend best practice improvements related to forklifts, tuggers, tugger carts and other material handling equipment.
Development of tugger or forklift routes that optimize material flow, while minimizing labor requirements.
Develop/Create/Update Long cycle standardize work instructions as required per new programs or updates.
Monitor Inventory ratio to detect opportunities to keep under target for all commodities.
Train operation members on DT report. Monitor DT to identify opportunities of classification to improve performance.
Support on inventory control reconciliation, cycle counts and Physical inventory.
Work closely with engineering on future plant expansions or production line enhancements to ensure lean and material flow best practices are implemented.
Develop, monitor and report out on Key Performance Indicators (KPIs). Responsible for development of corrective actions for KPIs not meeting goals.
Coordination with production and material planners to drive measurable improvements in inventory levels, warehouse footprint, on-time delivery performance, and lead-times through improved planning improvements.
Support in development of the Layout Management System processes and use the established processes to communicate any required updates to the layout of equipment, materials, workspace, etc.
Develop and implement 5S and visual factory control throughout the plant.
Perform Layered Process Audits in production as required.
Maintain 5S standards in workspace / department and hold team accountable for meeting 5S standards.
Perform other duties as required.
Who we are looking for
Bachelor Degree in Industrial Engineering or Supply Chain Operations Management, a related technical discipline, or 10 years related experience with a sound understanding and proven history of application of industrial engineering concepts.
Strong change management, facilitation, and communication skills coupled with a demonstrated ability to drive improvement in a highly decentralized environment.
Proven project management skills dealing with complex projects.
Strong computer skills including Microsoft Outlook, Excel, Power Point, Project, Word, CAD.
Strong leadership skills.
Your preferred qualifications
What we offer
At Magna, you can expect an engaging and dynamic environment where you can help to develop industry-leading automotive technologies. We invest in our employees, providing them with the support and resources they need to succeed. As a member of our global team, you can expect exciting, varied responsibilities as well as a wide range of development prospects. Because we believe that your career path should be as unique as you are.
Site Benefits
Medical, Dental, Vision
401K - matching
Paid vacation
Paid holidays
Employee profit sharing
Employee appreciation events
On-site cafeterias
Awareness. Unity. Empowerment.
At Magna, we believe that a diverse workforce is critical to our success. That’s why we are proud to be an equal opportunity employer. We hire on the basis of experience and qualifications, and in consideration of job requirements, regardless of, in particular, color, ancestry, religion, gender, origin, sexual orientation, age, citizenship, marital status, disability or gender identity. Magna takes the privacy of your personal information seriously. We discourage you from sending applications via email to comply with GDPR requirements and your local Data Privacy Law.