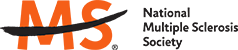
Job Information
Amcor Rigid Packaging Maintenance Lead - Injection Molding in Allentown, Pennsylvania
Reference #: REQ_58220 We are global, we are impacting the lives of millions every day, we are making a difference! At Amcor we are inspired to change the packaging industry and are taking on the aspirational challenge to make all our products recyclable or reusable by 2025. Through our products and global footprint, we are in a unique position to truly make a difference in the packaging space. Our products impact the lives of millions of people across the globe every day from food, beverage, pharmaceutical, medical, home- and personal-care, and other essential products. Amcor is a thriving S&P 500 organisation listed both on the NYSE (AMCR) and ASX (AMC) with US$13 billion in sales. We have a proud history dating back to the 1860's and come a long way from a single paper mill based in Melbourne to becoming the global leading packaging company. Today, Amcor is an international organisation empowering its 50,000 employees in over 40 countries and across 250 sites.
Will you be next to join our journey towards a more sustainable future?At Amcor we are always looking for talented and passionate individuals who are motivated to make a difference. Working at Amcor means you will have a unique opportunity to be a part of an organisation that is committed to providing sustainable packaging solutions. To find out more about our commitment to sustainability and about Amcor, visitwww.amcor.com.
Job Description
Title: Lead Maintenance Technician - Injection
Job Summary: Primary Purpose
Directly responsible for the maintenance, repairs, installation and improvement of all injection equipment. Managing and developing their maintenance team under the direction of the Maintenance Manager is essential. Works closely with the Injection Maintenance Manager and Process Engineer in development of management skills and knowledge of the business.
ESSENTIAL FUNCTIONS AND RESPONSIBILITIES Is responsible for directing their team in daily assigned jobs. Works well with their team members as well as employees in other departments and the production team. Can make tactical decisions based on situational conflicts and machine priorities. Can delegate jobs to their team members in order to meet the needs of the company. Is aware of plant priorities on a daily basis. Carries a radio at all times to communicate effectively with their team members as well as the production floor. Follows the rules set forth by the "Radio Code of Conduct". Understands that the maintenance internal customer is the production team. The maintenance team is here to support the production team in order to meet the needs of our external customers. Manages the PM's and parts for their assigned lines. Keeps track of the machines performance and actively strives to increase its productivity. Makes sure that the PM paperwork is fully filled out on the hard copy as tasks are completed. Fills the paperwork out in FMS and marks it as complete. Accurately documents all of the work performed during the PM both on the PM paperwork and in the FMS logbook. Creates work orders for parts, tasks and issues that were not addressed but need to be done on the next PM. Daily looks at the open work orders in FMS. Closes out work orders in a timely manner. Updates work orders with part numbers and requisition numbers. Works closely with the purchasing team on tracking these parts and putting them in a "kitting" location until all parts are received to complete the work order. Is involved in the scheduling of PMs. Tracks when major PMs (ei annual, quarterly) are due and plans for what needs to be done. Performs weekly PM Audits. Creates requisitions for parts in SAP. Contacts vendors for pricing. Works with the purchasing team in obtaining SAP numbers for parts that need to be stocked. Works closely with the purchasing team on keeping parts stocked that are required. Helps organize the stock room so that it is arranged in a manner that makes sense. Develops a "Critical/Consumable" p rts audit for their lines. Participates in SMED events and strives to hit the goal times that are set for each changeover. Updates, and creates change over sheets. Prints out these sheets for every changeover and verifies that it is accurate. Follows the changeover expectation guidelines. Is focused on continuous improvement. Is a point of contact for aftermarket vendors that provide cost saving and machine performance improvements. Can cross the wall and help the injection team when their job is complete. Can assist with changeovers and PMs in order to minimize downtime. Participates in the 13 week New Hire Training Program. Train level 1,2 and 3 mechanics on regular basis. Creates BIC Work Instructions for new tasks that employees tend to struggle with. Follows and enforces BIC standards to optimize their performance as well as their team members. Before leaving work each day, checks in with their department supervisor or manager. Makes sure that machines are running efficiently or are passed on to an individual who can repair the machine in a timely manner. Sets the example of what it means to work safe. Completes the monthly CBT and red card/green cards on time on each month. Ensures that their team members are completing their monthly safety obligations. Is focused on creating a quality container. Works closely with the process technicians to ensure that Amcor's quality standards are being upheld. Abides by and enforces Amcor's GMP policies.
LEAD RESPONSIBILITIES Direct lead for their changeover/PM team members.
QUALIFICATIONS Education:
Required: High School Diploma or GED equivalent Preferred: Technical School Diploma
Experience: Minimum 5 years' experience of industrial maintenance experience in a manufacturing environment with injection equipment Must have good working knowledge of high production machinery and facilities together with proven managerial experience. Ability to read, analyze and interpret general business reports and correspondence. Ability to define problems, collect data, establish facts, and draw valid conclusions. Ability to interpret an extensive variety of instructions and customer needs. Ability to work under pressure and interact with others. Ability to meet / exceed deadlines. Strong interpersonal skills including ability to communicate quickly and effectively with all members of the shift and management. Excellent verbal and written communication skills Proficient in electronic data-entry
Physical Requirements: Lift / push / pull up to 100 pounds 50 feet using a hydraulic hand jack (this is the equivalent of a static push / pull of approximately 70 pounds). Maximum frequent lifting weight of 75 pounds from ground to 6 feet overhead. Occasional frequency of lifting up to 100 pounds from ground to 6 feet overhead. Maximum frequent carrying weight of 60 pounds for 10 feet. Employees are required to stand / walk for up to 11 hours per shift on a concrete floor. Employees must be able to work 12-hour shifts day or nights, including weekends and holidays. Employees are required to bend; turn / twist; kneel; squat; crawl; climb; reach out and up; turn wrist; grasp; pinch; and have finger manipulations.
Required Safety Equipment: Employees are required to continuously wear hearing and eye protection, as well as protective clothing including steel toe shoes. Employees must wear hard hats during operation of cranes or man-lifts.
OurExpectations We expect our people to be guided by The Amcor Way and demonstrate our Values every day to enable the business to win. We are winning when: Our people are engaged and developing as part of a high-performing Amcor team Our customers grow and prosper from Amcor's quality, service, and innovation Our inv