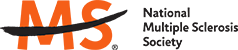
Job Information
Eaton Corporation Manufacturing / Process Engineer in Airdrie, Alberta
Eaton’s ES AMER PCS CA division is currently seeking a Manufacturing / Process Engineer. This position is based in our Airdrie, AB office and requires on-site presence.
What you’ll do:
Position Overview:
Under the direction of the Operations Manager, this position is responsible for designing, implementing and optimizing industrial processes including manufacturing flow, material and tools, required in order to improve value added activities on the production floor.
Making what matters work at Eaton takes the passion of every employee around the world. We create an environment where creativity, invention and discovery become reality, each and every day. It’s where bold, bright professionals like you can reach your full potential—and where you can help us reach ours.
In this function you will:
• Design, implement, and optimize industrial processes focusing on ensuring efficiency, quality, and safety throughout the production process. Maintenance of line for all products. Includes updating standard operations procedures and ECN.
• Determine manufacturing methods, tools and machines required to produce parts including assemblies and sub-assemblies. Implement I4.0 process and systems.
• Identification and implementation of process improvements.
• Instruct and train manufacturing personnel on new or revised manufacturing methods, tools and equipment.
• Responsible to define standard work by doing time studies including implementation of full analysis for VA, SVA and NVAA methodology as well as SPC and capability studies.
• Define manufacturing flow including safety, sequence, balance, parts and manpower requirements by implementing MURI, MURA, MUDA Methodology.
• Apply Lean and Six Sigma methodologies and tools to crate Process Maps, Layout, Plant Capacity (man vs installed capacity), Standard Work, Takt Times, Potential Failure Modes and Effects Analysis, Design of Experiments, Control Plans, and Job Safety Analysis for production lines.
• Define time required to manufacture all parts for a product line or a section based on the most economical methods developed through manufacturing planning in conjunction with methods, tools, work, plant layouts, and design engineering.
• Implement of cost reduction opportunities by doing analysis based on SVA and NVAA techniques.
• Implement and drive Root Cause Analysis based on potential poor of quality or Parts and processes.
• Implement Process and Quality meeting, Reporting and trends to review opportunities and concerns, including reporting and Root Cause updates.
• Safety responsibilities include safety and housekeeping objectives; follow all safety rules and procedures and report unsafe conditions to line management.
Qualifications:
Required (Basic) Qualifications:
• Bachelor’s degree in engineering.
• Minimum of 5 years of experience required in manufacturing engineering capacity.
• Experience using Continuous Improvement methodologies.
• Legally authorized to work in Canada without company sponsorship now and in the future.
• No relocation provided – candidate must reside within 80km of Airdrie, Alberta.
Preferred Qualifications:
• Strong working knowledge of LEAN Manufacturing processes and Six Sigma tools.
Skills:
Position Success Criteria:
• Ability to multi-task and work in a fast paced/changing environment.
• Excellent communication, interpersonal and organizational skills.
• Intermediate knowledge of MS Office.
• Strong analytical aptitude and complex problem-solving skills.
• Effective time management and project management skills.
• The ability to listen and understand problems presented while exchanging thoughts concerning possible solutions. When transmitting information to superiors one must be able to explain in detail the problem and methods of solution.
Eaton has in place accessibility policies for accommodating employees with disabilities. If you are selected for an interview and require accommodations, please let the recruiter or hiring manager know so that we can work to make reasonable adjustments that best suit your needs. Accessibility information may be found at: http://www.eatoncanada.ca/EatonCA/OurCompany/Accessibility/index.htm
We make what matters work. Everywhere you look—from the technology and machinery that surrounds us, to the critical services and infrastructure that we depend on every day—you’ll find one thing in common. It all relies on power. That’s why Eaton is dedicated to improving people’s lives and the environment with power management technologies that are more reliable, efficient, safe and sustainable. Because this is what matters.
We are confident we can deliver on this promise because of the attributes that our employees embody. We’re ethical, passionate, accountable, efficient, transparent and we’re committed to learning. These values enable us to tackle some of the toughest challenges on the planet, never losing sight of what matters.
We are committed to ensuring equal employment opportunities for job applicants and employees. Our recruitment processes use balanced selection criteria and avoid unlawful discrimination against applicants on the basis of their age, colour, disability, marital status, national origin, gender, gender identity, genetic information, race or racial origin, religion, sexual orientation or any other status protected or required by law.
Eaton Corporation
-
- Eaton Corporation Jobs